Дипломная работа: Проект централізованого технічного обслуговування маршрутних транспортних засобів на базі філії "ТЕМП-АВТО" відкритого акціонерного товариства "РІВНЕ-АВТО"
ДИПЛОМНИЙ ПРОЕКТ
НА ТЕМУ:
«ПРОЕКТ ЦЕНТРАЛІЗОВАНОГО ТЕХНІЧНОГО
ОБСЛУГОВУВАННЯ МАРШРУТНИХ ТРАНСПОРТНИХ ЗАСОБІВ НА БАЗІ ФІЛІЇ «ТЕМП-АВТО»
ВІДКРИТОГО АКЦІОНЕРНОГО ТОВАРИСТВА «РІВНЕ-АВТО»
Рівне 2010
Вступ
Технологічне оснащення ремонту автомобілів
і агрегатів є важливою ланкою в системі відновлення експлуатованої техніки. Для
реалізації необхідних ремонтних впливів у повному об’ємі потрібна наявність
широкої гами технологічних засобів, оптимальної по номенклатурі і по своїх
характеристиках.
В умовах ринкової економіки при
роздержавленні і приватизації машинобудівних підприємств частина номенклатури
обладнання виявилася незатребуваною по економічним та організаційно-технічний
причинам, а випуск нових зразків, необхідних реорганізованим ремонтним
підприємствам, дотепер не налагоджений.
У зв'язку з викладеним, у даний час дуже актуальним є проблема
створення такої системи ТОРМА, що характеризувалася б науковою обґрунтованістю,
оптимальністю й ефективністю використання при сформованому економічному укладі.
Ця система може бути сформована при наявності класифікаційних груп об'єктів
ремонту й однотипних ремонтно-технологічних процесів; мінімально потрібної
номенклатури і раціональних параметрів рядів технологічного устаткування.
На ремонтно-обслуговуючих підприємствах намітилася й інша
тенденція – сполучення випуску ремонтної і промислової продукції. Це не просте
підсумовування обсягів робіт, а перехід на якісно нову організацію виробництва.
Впровадження індустріальних методів істотно впливає на підвищення якості ремонту,
дозволяє більш повно використовувати новітні досягнення науки.
Обов'язковою умовою фірмового ремонту та
технічного обслуговування є використання технічної документації
заводу-виготовлювача. Ця обставина дозволяє забезпечувати єдність технології
виготовлення і високоякісного ремонту найбільш розповсюджених марок автомобілів
та проведення операцій по їх ТО у відповідності до нормативної документації, що
покращує експлуатаційні властивості автомобілів та підвищує безпеку руху.
Вітчизняний і закордонний досвід показує,
що ремонт автомобілів необхідний для повного використання їхнього ресурсу.
Існування ремонтного виробництва об'єктивно обумовлено, з одного боку, різною
надійністю складових частин автомобіля, а з іншого боку – можливістю ефективно
відновлювати їхні втрачені споживчі властивості.
Економічна доцільність ремонту
підтверджується структурою витрат на його виконання. При виготовленні нових
машин 70–80% витрат йде на придбання матеріалів і комплектуючих виробів, а при
капітальному ремонті – тільки 20–30%.
В останні роки в
зв'язку з впровадженням у виробничих організаціях та станціях технічного
обслуговування агрегатно-вузлового методу при поточних ремонтах автомобілів і
створенням відповідних обмінних фондів змінилася стратегія відновлення їх
працездатності на ремонтних підприємствах. У результаті істотно скоротився
повнокомплектний ремонт і значно збільшився обсяг спеціалізованого ремонту
агрегатів і відновлення деталей, використовуваних для поповнення обмінних
фондів.
На
ремонтно-обслуговуючих підприємствах намітилася й інша тенденція – сполучення
випуску ремонтної і промислової продукції. Це не просте підсумовування обсягів
робіт, а перехід на якісно нову організацію виробництва. Впровадження
індустріальних методів істотно впливає на підвищення якості ремонту, дозволяє
більш повно використовувати новітні досягнення науки.
Разом з тим, продукція
ремонтного виробництва значно менш однорідна, чим машинобудівного, границі
припустимих відхилень ширше, потенційна надійність відремонтованого об'єкта
залежить від сукупності великого числа перемінних факторів.
Відмітною рисою
ремонтного виробництва в західних країнах є широке впровадження фірмового
ремонту автомобілів і агрегатів. Ремонт здійснюється на ремонтних підприємствах
фірм-виготовлювачів нових машин, самостійними фірмами-посередниками і
невеликими вузько спеціалізованими ремонтними заводами.
Обов'язковою умовою фірмового ремонту та
технічного обслуговування є використання технічної документації
заводу-виготовлювача. Ця обставина дозволяє забезпечувати єдність технології
виготовлення і високоякісного ремонту найбільш розповсюджених марок
автомобілів.
Застосування нового механізованого технологічного обладнання та
впровадження нових технологій в процесі ремонту автомобілів в цілому та їх
агрегатів дозволяє знизити витрати на ремонт та зробити продукцію ремонтного
виробництва конкурентоспроможною в умовах ринкової економіки.
Метою даного дипломного проекту є розширення сфери діяльності
станції технічного обслуговування філії «ТЕМП-АВТО» Відкритого Акціонерного
Товариства «Рівне-АВТО» шляхом організації централізованого технічного
обслуговування маршрутних транспортних засобів, використовуючи
ремонтно-обслуговуючу та виробничу базу даного підприємства.
1. Організаційно-розрахункова
частина
1.1 Загальні відомості
про філіал «Темп-Авто»
Проектом передбачається реконструкція в
існуючих об'ємах будівлі СТО ВАТ «Рівне-Авто» по вул. Відінській, 9-а в м.
Рівне під центр по обслуговуванню автомобілів української автомобільної
корпорації «УкрАвто». Проектований центр надасть можливість розширити та якісно
вдосконалити Рівненську мережу станцій сервісного обслуговування автомобілів,
перейти на найновіші технології та обладнання, підвищити якість продукції та
послуг.
1.1.1 Генеральний план
і благоустрій
Площа орендованої ВАТ
«Рівне-Авто» земельної ділянки становить 0,8365 га. Передбачено додаткове
виділення земельної ділянки загальною площею 0,2347 га для влаштування
рекламних пілонів і стоянок гостьових автомобілів та автомобілів передпродажної
підготовки на відстані 10 м від будівлі, що підлягає реконструкції.
Головним фасадом
проектований центр обслуговування автомобілів зорієнтований на вул. С. Бандери.
Заїзд на територію центру передбачено з існуючого проїзду, виїзд – на вул. С. Бандери.
Ширина заїзду та виїзду – 5 м, радіуси заокруглень прийнято не менше 5,0 м.
Навколо будівлі передбачено круговий проїзд шириною 3,5–5,0 м для пожежних
автомобілів.
1.1.2
Архітектурно-планувальні та технологічні рішення
Реконструкції підлягає
корпус №2 СТО ВАТ «Рівне-Авто» по вул. Відінській в м. Рівне.
Об'ємно-планувальне рішення, склад і площі приміщень проектованого центру по
обслуговуванню автомобілів прийнято відповідно до завдання на проектування,
вимог замовника щодо корпоративного стилю та конструктивних особливостей існуючої
будівлі СТО.
Існуюча одноповерхова
будівля СТО в плані має форму прямокутника із розмірами 30x42 метри із
одноповерховими добудовами різної площі та функціонального призначення.
Передбачається демонтаж цих добудов та використання частини існуючих підвалів
під приміщення інженерно-технічного призначення.
Проектом реконструкції
передбачено необхідний набір приміщень для нормального функціонування центру:
зал передпродажної підготовки, виробничі та складські приміщення,
адміністративні, побутові та приміщення інженерно-технічного призначення. У
виробничій зоні передбачено чотири пости ТО та ТР, два пости дообладнання, пост
діагностики та тюнінг, що комплектуються необхідним технологічним обладнанням.
В центральній частині даного приміщення ескізним проектом передбачено
влаштування зенітних ліхтарів. Виробнича зона має зручні зв'язки із складом
запчастин, побутовими та адміністративними приміщеннями. Проектом
передбачається візуальний зв'язок між холом для очікування клієнтів і
виробничою, складською зоною та столом замовлень. Також, на вимогу замовника,
проектом передбачаються скляні перегородки між офісними приміщеннями, між
приміщенням передпродажної підготовки та виробничою зоною.
Перелік приміщень
корпусу №2 наведено в табл. 1.1.
Таблиця
1.1. Перелік приміщень корпусу №2
№ |
Назва |
Площа,
м2
|
1 |
Тамбур |
7,07 |
2 |
Приміщення
передпродажної підготовки |
522,46 |
3 |
Кабінет
директора |
11,27 |
4 |
Кабінет
для клієнтів |
4,49 |
5 |
Операційна
каса |
4,37 |
6 |
Коридор |
11,49 |
7 |
Жіночий
санвузол |
3,30 |
8 |
Чоловічий
санвузол |
5,26 |
9 |
Гарантійна
група |
7,48 |
10 |
Серверна,
приміщення інженерно-технічного працівника |
6,96 |
11 |
Тамбур |
2,83 |
12 |
Душева |
4,84 |
13 |
Санвузол
персоналу |
6,06 |
14 |
Гардероб
персоналу |
18,44 |
15 |
Кімната
персоналу |
18,22 |
16 |
Кімната
майстрів |
12,54 |
17 |
Виробниче
приміщення |
412,97 |
18 |
Склад
запчастин |
70,75 |
19 |
Хол
для очікування клієнтів |
16,91 |
20 |
Стіл
замовлень |
34,76 |
21 |
Кімната
охорони |
7,72 |
22 |
Санвузол
персоналу |
4,21 |
23 |
Інструментальна |
9,43 |
24 |
Щитова |
2,90 |
25 |
Насосна |
33,00 |
26 |
Вузол
вводу |
11,39 |
27 |
Вентиляційна |
15,51 |
28 |
Тамбур |
4,23 |
Характерний фірмовий
дизайн використані при проектуванні фасадів – скляний тамбур, козирок головного
входу із хромованими конструкціями, колонами та прозорим покриттям сотовим
полікарбонатним пластиком, лінійна система засклення головного та частини бокових
фасадів та оздоблення сріблястими алюмінієвими композитними панелями – створюють
образ корпоративного центру, що пізнається відразу. Логотипи автомобільних
бреднів та фірмові логотипи відображені на головному фасаді, на прапорах,
світлових рекламних пілонах та щитах візуально заздалегідь попереджують про
відкриття нового корпоративного центру.
Орієнтовні техніко-економічні показники по
виробничому корпусу наведені в табл. 1.2–1.3.
Таблиця 1.2. Орієнтовні
техніко-економічні показники по виробничому корпусу
№
п/п |
Назва |
Площа,
м2
|
1 |
Загальна
площа |
1322,87 |
2 |
Корисна
площа |
1268,36 |
3 |
Розрахункова
площа |
1159,55 |
4 |
Виробнича
площа |
412,97 |
5 |
Будівельний
об’єм |
6700 |
Таблиця 1.3. Техніко-економічні
показники по виробничому корпусу №2
№ п/п |
Найменування |
Одиниця виміру |
Кількість |
Примітка |
1 |
2 |
3 |
4 |
5 |
1. |
Потужність |
кількість постів |
8 |
|
2. |
Кількість поверхів |
поверх |
1 |
|
3. |
Загальний будівельний об'єм, в т.ч. |
м3
|
6700.00 |
|
|
підвалу |
м3
|
175.00 |
|
4. |
Площа забудови |
м2
|
1300.00 |
|
5. |
Загальна площа в т.ч. |
м2
|
1322.87 |
|
|
підвалу |
м2
|
64.13 |
|
6. |
Корисна площа |
м2
|
1268,36 |
|
7. |
Розрахункова площа |
м2
|
1159.55 |
|
8. |
Кількість обслуговуючого персоналу |
осіб |
24 |
|
9. |
Питома теплова потужність опалення |
Вт/м2
|
188 |
|
10. |
Питоме річне теплоспоживання: |
ГДж/м2 рік
|
0,69 |
|
11. |
Річна потреба в тепловій енергії |
Гкал/рік |
604,4 |
|
12. |
Річна потреба в електричній енергії |
тис. кВт/год |
183 |
|
13. |
Річна потреба в воді |
м3/рік
|
1401,6 |
|
1.1.3 Конструктивні
рішення
Існуюча будівля СТО трьох
прольотна, одноповерхова, прямокутна в плані. Під частиною будівлі розміщено
підвальні приміщення; в межах висоти будівлі влаштовано вбудований 2-й поверх.
Конструктивна схема
будівлі комбінована. Будівля має неповний каркас з поперечним розташуванням
ригелів, на котрі опираються панелі покриття. Ригелі – двоскатні збірні залізобетонні
балки покриття довжиною 18 м.
Покриття – із збірних
залізобетонних ребристих панелей, що опираються на балки покриття і на зовнішні
цегляні стіни.
1.2 Загальні положення
про діяльність філіалу
1.2.1 Види діяльності
філіалу
Філіал Відкритого акціонерного
товариства «Рівне-Авто» «Темп-Авто» (надалі іменується – Філіал) створено за
рішенням Загальних зборів акціонерів ВАТ «Рівне-Авто», надалі іменується – Товариство,
(протокол №1 від 12 квітня 2001 р.).
Місцезнаходження
Філіалу: Україна, м. Рівне, вул. Віденська, 9а.
Філіал є відособленим
підрозділом Товариства і в своїй діяльності керується законодавчими актами
України, Статутом Товариства, наказами, розпорядженнями та рішеннями органів управління
та/або посадових осіб Товариства, цим Положенням та внутрішніми документами
Товариства.
Філіал є суб'єктами
господарювання, що здійснюють свою діяльність від імені Товариства, без статусу
юридичної особи, має самостійний баланс, здійснює бухгалтерський облік, має
поточний та інші рахунки у національній та іноземних валютах в установах
українських та іноземних банках, печатку з найменуванням Товариства та своїм
найменуванням на українській мові, штампи Печатки та штампи можуть мати також
зображення знаку для товарів та послуг Товариства.
Товариство відповідає по
зобов'язанням Філіалу згідно із законодавством України та внутрішніми
документами Товариства.
За рішенням органу
управління Товариства на Філіал може бути покладено виконання окремих
зобов'язань Товариства.
Предметом діяльності Філіалу є:
діяльність пов'язана з
наданням послуг по обслуговуванню, ремонту і діагностиці транспортних засобів;
проведення інструментального контролю
технічного стану транспортних засобів;
метрологічне
забезпечення і ремонт засобів технічного діагностування на дочірніх підприємствах,
філіалах та представництвах Товариства, інших суб'єктів господарювання;
виконання
електровимірювальних робіт і проведення електричних іспитів та перевірок на
електроустаткуванні до 1000 В;
діяльність з придбання
та продажу на території України лакофарбних матеріалів та інших товарів;
купівля (придбання),
продаж, передання в оренду, лізинг тощо обладнання та технологій з виготовлення
лакофарбової продукції та фарбування транспортних засобів;
діяльність, пов'язана з
реалізацією транспортних засобів та номерних агрегатів, котрі підлягають
реєстрації та обліку у ДАІ МВС України, проведення аналізу стану якості,
надійності автомобілів у гарантійний та післягарантійний період., участь в
розробці заходів з підвищення якості та надійності транспортних засобів, та
номерних агрегатів;
торгівля транспортними
засобами, номерними агрегатами,
прокат транспортних
засобів та автомобільної техніки;
надання послуг по
зберіганню транспортних засобів;
комплексне передпродажне
обслуговування транспортних засобів, та номерних агрегатів;
гарантійне
обслуговування транспортних засобів, та номерних агрегатів; технічне
обслуговування та ремонт транспортних засобів, та номерних агрегатів, за межами
гарантійного терміну обслуговування;
торгівельна діяльність
щодо реалізації (торгівлі) обладнання автомобілів, запасних частин,
автоприналежностей, товарів народного вжитку та інших товарів, в тому числі на
консигнаційній та комісійній основі;
страхова діяльність,
зокрема щодо страхування транспортних засобів;
організація та
експлуатація платних автостоянок;
маркетингові,
консалтингові, та інші послуги;
внутрішні та міжнародні
перевезення пасажирів і вантажів автомобільним транспортом;
надання
транспортно-експедиційних послуг, в тому числі під час перевезень
зовнішньоторговельних і транзитних вантажів;
інша діяльність, не
заборонена законодавством України.
1.2.2 Господарська,
економічна та соціальна діяльність філіалу
Основним узагальнюючим
показником фінансових результатів господарської діяльності Філіалу є чистий
прибуток (доход).
Філіал не є самостійним
платником податку на прибуток. Податок на прибуток від діяльності Філіалу
сплачується консолідовано Товариством.
Філіал є самостійним
платником податку на додану вартість та самостійно сплачує інші податки, збори,
обов'язкові платежі згідно чинного законодавства в порядку, встановленому
наказами та розпорядженнями Генерального директора Товариства.
Генеральний директор
Товариства затверджує основні планові показники щодо виробничо-господарської
діяльності Філіалу. На підставі вказаних показників Генеральний директор
Товариства затверджує план виробничої діяльності Філіалу та забезпечує
доведення вказаного плану до Філіалу. План затверджується на рік, з розбивкою
по кварталах з урахуванням фактичних виробничих потужностей та введення в дію нових
виробничих потужностей; розрахункові показники плану визначаються за
методологією, прийнятою в Товаристві. Плановий та фактичний розмір чистого
прибутку, обігових коштів та витрат на технічне переоснащення розподіляється централізовано
за рішенням Генерального директора Товариства. Трудовий колектив Філіалу
складають всі громадяни, які своєю працею беруть участь у його діяльності на
підставі трудового договору. Інтереси трудового колективу представляє
профспілкова організація Товариства.
1.2.3 Санітарно-технічна
частина
Опалення центру
обслуговування автомобілів (корпус №2 ВАТ «Рівне – АВТО) здійснюватиметься
централізовано за незалежною схемою підключення. Теплова потужність систем
опалення будівлі складає 58 кВт.
Питома теплова
потужність – 30 Вт/м.
Річні витрати тепла на
опалення – 96,4 Гкал/рік.
Питоме теплоспоживання –
0,2 ГДж/м2 рік.
Корисна площа приміщень
центру обслуговування автомобілів – 1262,28 м.
В будівлі запроектовані
три системи опалення:
– система опалення
для приміщення передпродажної підготовки;
– система опалення
для виробничого приміщення;
– система опалення
адміністративно-побутових приміщень.
Теплоносій – вода для
всіх систем готується в одному пластинчатому теплообміннику, що знаходиться в
тепловому вузлі, далі подається на розподільчу гребінку, яка розділяє систему
опалення на три гілки системи.
В якості нагрівальних
приладів прийняті конвектори з природною конвекцією зі спареним
теплообмінником, що монтуються врівень підлоги.
Передбачатиметься загальнообмінна
вентиляція, розрахована на розчинення газоподібних шкідливостей. В приміщенні
передпродажної підготовки припливне повітря подаватиметься зверху вниз
зосередженими струменями, у виробничому приміщенні – розосереджено в робочу зону,
в адміністративно-побутових приміщеннях неорганізований приплив повітря через
фрамуги вікон.
В автосалоні
передбачено витяг повітря з механічним спонуканням, яке буде забиратися з
верхньої зони. У виробничому приміщенні видалення повітря проектуватиметься з
верхньої і нижньої зон порівну. В інших приміщеннях – витяжка з природнім
спонукання, крім санвузлів, де встановлюватимуться канальні вентилятори
побутового призначення. Видалення повітря з автосалону і виробничого приміщення
здійснюватиметься зосереджено, даховими вентиляторами.
Припливними системами
передбачається підтримання заданої температури повітря у приміщенні, що
забезпечується автоматикою, яка встановлюється в системі теплопостачання
калориферів припливних систем, регулювання температури теплоносія, який
подається до калориферів припливних систем. В нашому випадку проектуватиметься
декілька окремих припливних систем вентиляції.
Повітропроводи
проектуються із тонколистової сталі по ГОСТ 19904–74* нормальні.
Ділянки транзитних
повітропроводів від припливних установок до приміщень, в які подається повітря,
для забезпечення межі вогнестійкості повітропроводів рівною 0,5 години,
ізолюються матами мінераловатними, прошивними, товщиною 70 мм, з покривним
шаром з алюмінієвої фольги.
Джерелом
теплопостачання калориферів центру обслуговування автомобілів є тепловий вузол.
Розрахункові параметри
теплоносія в системах теплопостачання калориферів – 90–70°С.
Трубопроводи монтуються
із стальних водогазопровідних труб ГОСТ 3262–75*.
Витрата тепла на
вентиляцію приблизно складає 306 кВт.
Річні витрати тепла на
вентиляцію складають – 236 Гкал/рік (982 ГДж/рік).
Джерелом водопостачання
центру обслуговування автомобілів служить існуюча вулична мережа водопроводу
д=300 мм.
Точкою підключення до
мережі вуличного водопроводу є існуючий водопровідний колодязь, в якому
встановлюватиметься запірна арматура. Тиск води в точці підключення становитиме
1,5–2,6 атм.
Розрахункова витрата
води на господарсько-побутові потреби центру складатиме 3,84 м3/добу.
Гаряче водопостачання
на господарсько-побутові потреби центру обслуговування автомобілів – централізоване.
Згідно з п. 6.1
СНиП 2.04.01–85, розрахункові витрати води на потреби внутрішнього
пожежогасіння центру становлять – 2x2,5 л/сек. Внутрішнє пожежогасіння
приміщень центру здійснюється від пожежних кранів <1=50 мм, що розташовані
на об'єднаній системі внутрішнього господарсько-питного та протипожежного
водопроводу згідно п. 6.13; 6.14 СНиП 2.04.01–85.
В приміщеннях
підготовки та виробничому приміщенні передбачаємо автоматичну спринклерну
систему пожежогасіння, що працює на воді, яка включає: насос (основний і
резервний), засувки з ручним приводом, зворотній клапан, прилад контролю і
управління, розподільний трубопровід, вузол управління спринклерною установкою,
спринклери, манометр контактний, компресор, пневмобак.
Спринклерна система
будівлі матиме основне і автоматичне джерела водопостачання: основне – зовнішня
водопровідна мережа, автоматичне – пневмобак.
Потреба у воді
становить 7,8 м3/год (час гасіння – 30 хв).
Відведення
господарсько-побутових та виробничих стоків від центру обслуговування
автомобілів здійснюється самопливною каналізацією в септик, що
проектуватиметься.
Розрахункові витрати
стічних вод – див. табл. 1.4.
Внутрішня система каналізації будинку
прокладається з пластмасових труб типу ПВХ (1=50; 110 мм за ТУ 6–19–307–86,
відповідно до вимог та розділу – 17 СНиП 2.04.01–85.
Таблиця 1.4. Витрати
води
№ п/п |
Найменування системи |
Витрати води |
Примітка |
|
|
м3 /добу
|
м3 /год
|
л/сек |
|
1. |
Загальне водоспоживання |
5,3 |
1,33 |
1,18 |
СНиП 2.04.01–85 дод. 3 (п. 20; 24) |
|
у тому числі:
а) холодне водопостачання (В1)
|
3,84 |
1,33 |
0,35 |
|
|
Б) гаряче водопостачання (ТЗ) |
3,84 |
1,33 |
0,35 |
|
|
В) полив прилеглої території |
- |
- |
0,3 |
|
2. |
Госп-побутова та виробнича каналізація (К1; К3) |
5,04 |
1,26 |
2,86 |
|
1.3 Розрахунок виробничої
програми по централізованому обслуговуванню маршрутних транспортних засобів
1.3.1 Коригування
нормативів технічного обслуговування та ремонту рухомого складу
Відповідно до завдання нам необхідно провести коригування
нормативів технічного обслуговування та ремонту мікроавтобусів Mercedes Benz
408D. Кількісний та якісний склад парку автотранспортних засобів, що підлягає централізованому
обслуговуванню наведений у табл. 1.5.
Таблиця 1.5. Кількісний та якісний склад парку автотранспортних
засобів що підлягає централізованому обслуговуванню
Марка
транспортного засобу |
Кількість
транспортних засобів з частиною пробігу до КР |
До
0,25 |
Понад
0,25 до 0,5 |
Понад
0,5 до 0,75 |
Понад
0,75 до 1,0 |
Понад 1,0
до 1,25 |
Понад
1,25 до 1,5 |
Понад
1,5 до 1,75 |
Понад
1,75 до 2,0 |
Понад
2,0 |
Всього |
Mercedes
Benz 408D |
15 |
10 |
20 |
25 |
10 |
30 |
40 |
20 |
15 |
185 |
Використовуємо нормативи періодичності технічного обслуговування
(ТО) і поточного ремонту (ПР) та трудомісткості:
-
для умов експлуатації другої
категорії;
-
базових моделей автомобілів;
-
помірного кліматичного
району;
-
автотранспортних
підприємств, де обслуговується 150 – 200 одиниць рухомого складу.
При коригуванні нормативів застосовуємо коригуючи коефіцієнти, які
враховують:
K1 – категорію умов експлуатації автомобілів;
K2 – модифікацію рухомого складу та організацію його роботи;
K3 – природно-кліматичні умови;
K4 та K4* – пробіг автомобіля з початку
експлуатації;
K5 – розмір АТП та кількість технологічно сумісних груп рухомого
складу.
Коригування здійснюють шляхом множення значення нормативів на величину
результуючих коефіцієнтів, які визначають як добуток окремих коефіцієнтів:
-
для періодичності ТО –
K1·K3
-
пробігу до КР –
K1·K2·K3
-
трудомісткості ТО –
K2·K5
-
трудомісткості ПР –
K1·K2·K3·K4·K5
-
витрат запасних частин – K1·K2·K5
Значення коефіцієнтів коригування приймаємо за таблицями з літературних
джерел [1, 2, 3]. Результуючі коефіцієнти коригування нормативів періодичності
ТО та пробігу до КР повинні бути не менші 0,5. Після визначення відкоригованої
періодичності ТО перевіряємо її кратність між видами ТО з подальшим
заокругленням до цілих сотень кілометрів.
Причому, коефіцієнти K4 та K4*,
що враховують пробіг автомобіля з початку експлуатації розраховуємо як середньо
вагові величини.
Для визначеного завданням автомобіля Mercedes Benz 408D значення
коефіцієнтів складають (див. додаток 13.5 – 13.8 [1]):
Коефіцієнт, що враховує категорію умов експлуатації автомобілів K1
= 0,8 (для періодичності ТО); K1 = 1,2 (для питомої трудомісткості
ПР); K1 = 0,8 (пробігу до КР); K1 = 1,25
(витрат запасних частин).
Коефіцієнт, що враховує модифікацію рухомого складу та організацію
його роботи K2 = 1,0 (для базових машин для коригування
трудомісткості ТО і ПР, пробігу до КР, витрат запасних частин).
Коефіцієнт, що враховує природно-кліматичні умови K3
= 1,0 (для помірного клімату при коригуванні періодичності ТО, питомої
трудомісткості ПР, пробігу до КР та витрат запасних частин).
Коефіцієнт, що враховує розмір АТП та кількість технологічно
сумісних груп рухомого складу K5 = 1,05.
Середньовагові величини коефіцієнтів K4 та K4*
розраховуємо за формулою:
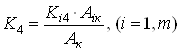
де m – число інтервалів пробігу до КР;
Кі4 – коефіцієнт, який відповідає і-му інтервалу пробігу з початку
експлуатації;
Аік - число автомобілів з
пробігом з початку експлуатації, що відповідає і-му інтервалу.
Для автомобіля Mercedes Benz 408D:


Відповідно до додатку 13.1 [1] для автомобілів Mercedes Benz 408D
нормативна періодичність ТО-1 складає 3000 км, нормативна періодичність ТО-2
складає 12000 км. Нормативний пробіг до КР 300000 км (див. додаток
13.2 [1]).
Розрахунки по коригуванню нормативів ТО і Р рухомого складу проводимо
в табличній формі. Результати розрахунків наведені в табл. 1.6 (у графі 4
приведені нормативні дані для базових автомобілів).
Таблиця 1.6. Результати коригування нормативів ТО і Р рухомого
складу (Mercedes Benz 408D)
Показники |
Одиниці
виміру |
Основний
норматив |
Значення коефіцієнтів
|
Результуючий
коефіцієнт |
Скориговане
значення нормативів |
K1
|
K2
|
K3
|
K4
|
K5
|
2 |
3 |
4 |
5 |
6 |
7 |
8 |
9 |
10 |
11 |
Періодичність |
|
|
|
|
|
|
|
|
|
ТО-1 |
км |
3000 |
0,8 |
|
1 |
|
|
0,8 |
2400 |
ТО-2 |
км |
12000 |
0,8 |
|
1 |
|
|
0,8 |
9600 |
Пробіг
до КР |
тис.
км |
300 |
0,8 |
1 |
1 |
|
|
0,8 |
240 |
Трудомісткість |
|
|
|
|
|
|
|
|
|
ЩО |
люд-год |
0,5 |
|
1 |
|
|
1,05 |
1,05 |
0,525 |
ТО-1 |
люд-год |
3,4 |
|
1 |
|
|
1,05 |
1,05 |
3,57 |
ТО-2 |
люд-год |
14,5 |
|
1 |
|
|
1,05 |
1,05 |
15,225 |
ПР |
(люд-год)/1000 км |
8,5 |
1,2 |
1 |
1 |
1,36 |
1,05 |
1,7129 |
14,56 |
Простій
під час |
|
|
|
|
|
|
|
|
|
ТО
і ПР |
дні/1000 км |
0,5 |
|
|
|
1,173 |
|
1,173 |
0,58 |
КР |
дні |
22 |
|
|
|
|
|
|
22 |
1.3.2 Розрахунок річної виробничої
програми по технічному обслуговуванню та ремонту рухомого складу
Кількість ТО і КР розраховуємо за сумарним річним пробігом за формулою:
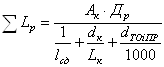
де Ак – облікова кількість автомобілів
однотипної моделі, одиниць (відповідно до завдання Ак = 185
автомобілів Mercedes Benz 408D);
Др – кількість робочих днів за рік (Др = 210 днів,);
lсд – середньодобовий пробіг автомобіля, (lсд = 180 км);
dк – кількість днів простою автомобіля під час КР, приймаємо 25
днів;
Lк – скоригований пробіг автомобіля до КР, км;
dТОіПР – тривалість простою під час ТО і ПР, дні/1000 км, приймаємо
по додатку 13.3 [1] dТОіПР = 0,5 дні/1000 км.
Таким чином, підставивши числові значення отримаємо:
км
Визначаємо за формулами річну кількість ТО і КР для автомобілів
Mercedes Benz 408D:
-
кількість капітальних
ремонтів 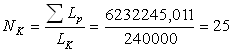
-
кількість ТО-2 
-
кількість ТО-1 
-
кількість ЩО 
-
кількість сезонних
обслуговувань СО
.
Результати розрахунків кількості технічних дій КР, ТО-2, ТО-1, ЩО
та сезонних обслуговувань заносимо в табл. 1.7, причому при розрахунках
кількості відповідних технічних дій як результат приймаємо тільки цілу частину
отриманого числа.
Таблиця 1.7. Результати розрахунків кількості технічних дій
КР, ТО-2, ТО-1, ЩО та сезонних обслуговувань
Модель
автомобіля |
Річна
кількість |
КР
(NK)
|
ТО-2
(NТО-2)
|
ТО-1
(NТО-1)
|
ЩО
(NЩО)
|
СО
(NСО)
|
Mercedes
Benz 408D |
25 |
624 |
1947 |
34623 |
370 |
Розраховуємо річні трудомісткості сезонного, другого, першого та щоденного
технічних обслуговувань та ПР за формулами:



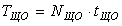
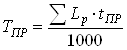
де m1 – частка трудомісткості ТО-2 яка припадає
на одне сезонне обслуговування (для помірного клімату m1 = 0,2);
Ак – облікова кількість автомобілів однотипної моделі, одиниць;
tЩО, t1, t2 – скоригована
нормативна трудомісткість відповідно щоденного, першого та другого технічних
обслуговувань, людино-годин;
tПР – скоригована нормативна трудомісткість поточного ремонту,
людино-годин/1000 км.
Підставивши числові значення, одержимо:
люд-год
люд-год
люд-год
люд-год
люд-год
Результати розрахунків трудомісткості технічних дій наведені в
табл. 1.8.
Таблиця 1.8. Результати розрахунків трудомісткості
технічних дій СО, ЩО, ТО-1, ТО-2 та ПР рухомого складу
Значення
параметрів |
Види
робіт по автомобілях Mercedes Benz 408D, людино-годин |
Основні
роботи |
Всього
по основних роботах |
1 |
2 |
3 |
Облікова кількість
автомобілів |
185 |
|
Кількість
ЩО |
34623 |
|
Зкоригована
трудомісткість ЩО, люд-год |
0,525 |
|
Трудомісткість
ЩО |
18177,075 |
18177,075 |
Кількість
ТО-1 |
1947 |
|
Зкоригована
трудомісткість ТО-1, люд-год |
3,57 |
|
Трудомісткість
ТО-1 |
6950,79 |
6950,79 |
Кількість
ТО-2 |
624 |
|
Зкоригована
трудомісткість ТО-2, люд-год |
15,225 |
|
Трудомісткість
ТО-2 |
9500,4 |
|
Кількість
сезонних обслуговувань |
370 |
|
Множник
m1·t2
|
3,045 |
|
Трудомісткість
сезонного обслуговування, ТС, люд-год
|
1126,65 |
|
Трудомісткість
ТО-2 + ТС
|
10627,05 |
10627,05 |
Річний
пробіг, км |
6232245,011 |
|
Зкоригована
трудомісткість ПР, люд-год/1000 км |
14,55981081 |
|
Трудомісткість
ПР |
90740,30829 |
90740,31 |
Сумарна
трудомісткість основних робіт, люд-год |
|
126495,22 |
Сумарна річна
трудомісткість ТО і ПР по одній моделі рухомого складу:

Підставивши числові значення, маємо:
люд-год
Трудомісткість діагностування входить до трудомісткості ТО і ПР за
видами робіт [3, 4].
Трудомісткість контрольно-діагностичних робіт ТО-1 (загальне
діагностування Д-1):
рульовий транспортний технічний обслуговування
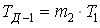
де m2 – частка трудомісткості ТО-1, яка припадає
на загальні діагностичні роботи (вибираємо з додатка 2 [1], m2
=0,1);
люд-год
Трудомісткість контрольно-діагностичних робіт ТО-2 (поглиблене
діагностування Д-2):
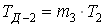
де m3 – частка трудомісткості ТО-2, яка припадає
на поглиблене діагностування (вибираємо з додатка 2 [1], m3 =0,1);
люд-год
Трудомісткість контрольно-діагностичних робіт ПР:

де m4 – частка трудомісткості ПР, яка припадає
на загальне та поглиблене діагностування (вибираємо з додатка 2 [1], m4
=0,02);
люд-год
люд-год
Допоміжні роботи становлять 30% сумарної трудомісткості ТО і ПР, якщо
АТП налічує до 200 одиниць транспортних засобів. До складу допоміжних робіт входять:
-
технічне обслуговування та
ремонт обладнання й інструменту;
-
транспортні та вантажно-розвантажувальні
роботи, пов’язані з ТО і Р рухомого складу;
-
перегін автомобілів в
середині автотранспортного підприємства;
-
зберігання, приймання та
видача матеріальних цінностей;
-
прибирання виробничих
приміщень та території і інші.
люд-год
В свою чергу, допоміжні роботи розподіляються наступним чином:
– по самообслуговуванню –
40…50%
– транспортні –
3…10%
– перегін автомобілів –
14…26%
– приймання, зберігання та видача матеріальних цінностей –
8…10%
– прибирання приміщень та території –
14…20%
Результати розрахунків по видах допоміжних робіт зводимо в табл.
1.9.
Таблиця 1.9. Результати розрахунків по видах допоміжних
робіт
Види
допоміжних робіт |
Самообслуговування |
Транспортні
роботи |
Перегін
автомобілів |
Приймання, зберігання та видача матеріальних цінностей |
Прибирання
приміщень та території |
Середня
частка виду робіт |
0,45 |
0,09 |
0,2 |
0,09 |
0,17 |
Трудомісткість
виду робіт, люд-год |
17076,9 |
3415,4 |
7589,7 |
3415,4 |
6451,3 |
Розподіл робіт ТО і ПР за видами робіт здійснюємо за даними
додатку 2 [1], а результати розподілу подаємо у вигляді табл. 1.10.
Таблиця 1.10. Результати розподілу робіт ТО і ПР за видами
робіт
№
п/п |
Вид
робіт |
Вид ТО чи ПР транспортного засобу |
Роботи
по самообслуговуванню |
Всього,
люд-год |
% |
люд-год |
% |
люд-год |
|
Туалетні
роботи |
|
|
|
|
|
1 |
прибиральні |
40 |
7270,83 |
|
|
7270,83 |
2 |
мийні |
10 |
1817,7075 |
|
|
1817,7075 |
|
Поглиблені
роботи |
|
|
|
|
|
3 |
прибиральні |
40 |
7270,83 |
|
|
7270,83 |
4 |
мийні |
10 |
1817,7075 |
|
|
1817,7075 |
|
Всього
по ЩО |
100 |
18177,075 |
|
|
18177,075 |
ТО-1 |
5 |
Загальне
діагностування (Д-1) |
10 |
695,079 |
|
|
695,079 |
6 |
Кріпильні,
регулювальні, змащувальні та інші роботи |
90 |
6255,711 |
|
|
6255,711 |
|
Всього
по ТО-1 |
100 |
6950,79 |
|
|
6950,79 |
ТО-2 |
7 |
Поглиблене
діагностування (Д-2) |
10 |
1062,705 |
|
|
1062,705 |
8 |
Кріпильні,
регулювальні, змащувальні та інші роботи |
90 |
9564,345 |
|
|
9564,345 |
|
Всього
по ТО-2 + ТС
|
100 |
10627,05 |
|
|
10627,05 |
ПР |
|
Постові
роботи |
|
|
|
|
|
9 |
Загальне
діагностування (Д-1) |
1 |
907,40 |
|
|
907,40 |
10 |
Поглиблене
діагностування (Д-2) |
1 |
907,40 |
|
|
907,40 |
11 |
Регулювальні
та демонтажно-монтажні роботи |
35 |
31759,11 |
|
|
31759,11 |
12 |
Зварювальні
роботи |
4 |
3629,61 |
|
|
3629,61 |
13 |
Жерстяницькі
роботи |
3 |
2722,21 |
|
|
2722,21 |
14 |
Малярні
роботи |
6 |
5444,42 |
|
|
5444,42 |
15 |
Деревообробні
роботи |
0 |
0,00 |
16 |
2732,30 |
2732,30 |
|
Всього
постові роботи ПР |
50 |
45370,15 |
|
|
48102,45 |
|
Роботи
на дільницях |
|
|
|
|
|
16 |
Агрегатній |
18 |
16333,2555 |
|
|
16333,26 |
17 |
Слюсарно-механічній |
10 |
9074,03 |
48 |
8196,89 |
17270,92 |
18 |
Електротехнічній |
5 |
4537,02 |
25 |
4269,21 |
8806,23 |
19 |
Акумуляторній |
2 |
1814,81 |
|
|
1814,81 |
20 |
Ремонт
приладів системи живлення |
4 |
3629,61233 |
|
|
3629,61 |
21 |
Шиномонтажній |
1 |
907,40 |
|
|
907,40 |
22 |
Вулканізаційній
(ремонт камер) |
1 |
907,40 |
|
|
907,40 |
23 |
Кувально-ресорній |
3 |
2722,20925 |
2 |
341,54 |
3063,75 |
24 |
Мідницькій |
2 |
1814,81 |
1 |
170,77 |
1985,57 |
25 |
Зварювальній |
1 |
907,40 |
4 |
683,07 |
1590,48 |
26 |
Жерстяницькій |
1 |
907,40 |
4 |
683,07 |
1590,48 |
27 |
Арматурній |
1 |
907,403083 |
|
|
907,40 |
28 |
Оббивальній |
1 |
907,403083 |
|
|
907,40 |
|
Всього
роботи ПР на дільницях |
50 |
45370,1541 |
84 |
14344,56 |
59714,71 |
|
Всього
роботи по ПР |
100 |
90740,31 |
100 |
17076,86 |
107817,16 |
|
Разом
виробничі
роботи
|
|
126495,22 |
|
17076,86 |
143572,08 |
Крім цього,
трудомісткість самообслуговування розподіляється по видах робіт, %:
– електротехнічні 25; –
механічні 32;
– слюсарні 16; –
ковальські 2;
– жерстяницькі 4; –
зварювальні 4;
– ремонтно-будівельні та столярні 16; – мідницькі
1.
Роботи механічні, слюсарні і трубопровідні об’єднуємо у
слюсарно-механічні, а ремонтно-будівельні та солярні – відносимо до
деревообробних.
Трудомісткість зварювальних, жерстяницьких і деревообробних робіт
визначається з врахуванням типу кузова транспортного засобу.
Дані розподілу використовуються для розрахунків показників зон,
постів і дільниць ТО і ПР.
Розподіл робіт ЩО наведено для виконання їх механізованим методом.
У табл. 1.10 наведений розподіл робіт по самообслуговуванню,
оскільки їх обсяг не перевищує 100000 люд-год. При більшій трудомісткості слід
передбачати окремо відділ головного механіка.
1.3.3 Розрахунок постів та ліній з ТО і
ПР
Добова програма кожного виду ТО визначається за формулою:

де і – вид технічного обслуговування (ЩО, ТО-1, ТО-2);
Nі – річна програма і-го виду ТО по всіх моделях автомобілів;
Др – кількість робочих днів за рік (згідно з завданням Др
= 210 днів).
Отже, добова програма кожного виду ТО:
– ТО-2 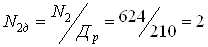
– ТО-1 
– ЩО 
1.3.4 Методи та організація виконання ТО
і ПР
Технологічний процес ТО і ремонту автомобілів – частина
виробничого процесу технічної підготовки автомобілів, що є сумою дій для зміни
розміру, форми, стану (внутрішніх властивостей) і взаємного розміщення
предметів праці (наприклад, процеси виконання ТО-1, ПР двигуна і т.д.).
Загальний технологічний
процес технічної підготовки автомобілів треба розглядати так. Прибуваючі
автомобілі проходять контрольно-пропускний пункт (КПП) і їх оглядає черговий
механік. При цьому він перевіряє комплектність і зовнішній вигляд автомобіля,
визначає його технічний стан, передусім механізмів, які створюють безпеку руху.
Після огляду справні автомобілі направляють у зону ЩО, а потім на зберігання. У
разі потреби деякі автомобілі після ЩО надходять у відповідні зони ТО і ГІР, а
потім на зберігання. Направляє автомобілі в ці зони черговий механік за планом-графіком
на ТО, а в зону ПР – за заявкою водія або за висновком чергового механіка.
Виявивши в процесі приймання рухомого складу пошкодження аварійного характеру,
складають спеціальний акт, який подається головному інженерові і є підставою
для пред'явлення матеріального позову винуватому. У разі передчасного повернення
рухомого складу з лінії з технічних причин черговий механік робить відмітку у
відповідній графі дорожнього листка і направляє автомобіль у ремонт.
Виявивши на лінії
несправність, водій викликає автомобіль технічної допомоги і черговий механік
виписує листок обліку на ремонт автомобіля на лінії, який потім передається
механікові технічної допомоги. Після усунення несправності заповнений механіком
автомобіля технічної допомоги листок обліку передається черговому механікові
контрольно-пропускного пункту.
Перед виїздом на лінію
водієві у диспетчерській видають дорожній листок, який він пред'являє
механікові контрольно-пропускного пункту і одержує дозвіл на виїзд. У багатьох
АТП черговий механік, щоб скоротити час виїзду автомобілів, оформляє дозвіл на
виїзд у дорожніх листках заздалегідь, до початку випуску рухомого складу.
Розглянемо організацію
виконання робіт на різних видах ТО. Порядок виконання робіт на ЩО визначений
«Правилами технічної експлуатації рухомого складу автомобільного транспорту».
Цей документ передбачає обов’язкове щоденне виконання контрольних робіт ЩО на
контрольно-пропускному пункті механіком при поверненні автомобілів із лінії. Правильна
організація цих робіт – перший важливий етап раціональної організації технологічних
процесів усіх видів ТО і ремонту.
Порядок огляду визначає
технічна служба АТП із урахуванням конструктивних особливостей використовуваних
на АТП автотранспортних засобів і діючих нормативів на їхнє обслуговування. При
ЩО обов'язково перевіряють стан агрегатів, вузлів і систем, які впливають на
безпеку руху. Особливо старанно діагностують ті елементи автомобілів у
таксомоторів і всіх автомобілів, які працюють на гірських маршрутах.
При найменшій разовій
трудомісткості і періодичності виконання ЩО має найбільшу питому (на 10 тис. км
пробігу) трудомісткість, яка приблизно дорівнює сумі питомих трудомісткостей ТО-1
і ТО-2. Природно, це потребує раціональної організації ЩО на АТП. Для спеціалізації
постів і засобів механізації ЩО як основні оцінні критерії виконуваних операцій
можна використовувати ступінь однорідності (характеризує однотипність операцій,
прийомів і способів виконання їх), спільність застосовуваного устаткування,
значущість робіт для створення безпеки руху автомобілів на лінії.
На підставі оцінних
критеріїв комплекс операцій ЩО можна поділяти на чотири групи:
перша група – контрольно-оглядові
операції. Ці прості операції виконують візуально (перевірка комплексності
автомобіля, його зовнішнього вигляду і т.д.);
друга група – контрольно-діагностичні
операції для перевірки вузлів, які впливають на безпеку руху, їх виконують за
допомогою засобів технічної діагностики (діагностування рульового керування,
гальмової системи та ін.);
третя група – прибирально-мийні
операції (прибирання кабіни або салону, миття і сушіння автомобіля);
четверта група – заправні
операції (заправка автомобіля паливом, маслами, охолодною рідиною).
Таким чином, якщо
виходити із спеціалізації робіт, то для виконання комплексу операцій ЩО треба
мати пости або дільниці, спеціалізовані на виконанні кожної групи операцій ЩО.
На контрольно-пропускному пункті треба виконувати операції тільки першої групи,
які не потребують застосування діагностичного устаткування. Тут після
повернення автомобілів із лінії виконують такі роботи: занесення до дорожнього
листка часу повернення ^автомобіля і показань спідометра; перевірка
комплектності автомобіля; огляд зовнішнього вигляду, виявлення відказів і
несправностей відповідно до карти огляду технічного стану автомобіля;
оформлення заявок водіїв на усунення несправностей і відказів, виявлених на
лінії і при огляді автомобілів на контрольно-пропускному пункті; перевірка
пломб на спідометрах; направлення автомобілів за графіком на діагностику.
Під час випуску
автомобілів на лінію на контрольно-пропускному пункті перевіряють: наявність і
правильність оформлення належної документації (дорожній листок, технічний
талон), відмітка в дорожньому листку про проходження передрейсового медичного
огляду); цілісність пломби на спідометрі; зовнішні й вигляд автомобіля та його
комплектність; справність вузлів і агрегатів, які впливають на безпеку руху,
якщо ці вузли і механізми ремонтувались у між змінний час.
Автомобілі, що
повернулися в АТП справними, при виїзді з підприємства повторно не перевіряють.
Після закінчення перевірки механік контрольно-пропускного пункту підписує
дорожній листок. У графі «Автомобіль технічно справний, виїзд дозволяється» він
записує час виїзду автомобіля за межі АТП.
Операції другої групи
виконують у спеціалізованих підрозділах експрес-діагностики, роль яких на АТП
повинні виконувати дільниці Д-1. Ці дільниці оснащують серійними засобами
технічної діагностики.
Дільниці
експрес-діагностики вирішують такі завдання: виявлення автотранспортних
засобів, технічний стан яких не відповідає вимогам безпеки руху; регулювання
вузлів, які впливають на безпеку руху, та контроль їх після виконання ТО-1, ТО-2
і ПР. Розробляють основні положення щодо організації на АТП еспрес-діагностування
(Д-1) вузлів, які впливають на безпеку руху, типаж ліній експрес-діагностування
автомобілів, типові планування з переліком устаткування, технологічні карти для
проведення експрес-діагностування, порядок застосування типової документації,
наведений у «Рекомендації щодо організації експрес-діагностування (Д-1)
автомобілів на АТП різної потужності».
Експрес-діагностування
технічного стану вузлів, які впливають на безпеку руху, – це
діагностування прискореними методами за обмеженою кількістю параметрів основних
механізмів і систем автомобіля, відкази яких можуть спричинити аварійні
ситуації, і виконання робіт для їх регулювання. Як самостійний вид
діагностування воно проводиться на станціях діагностування Державтоінспекції.
На АТП Д-1
розглядається як заключний вид дії після виконання ТО-1, ТО-2 і ПР автомобілів.
При виявленні на Д-1
несправностей, які не можна усунути регулюванням, автобус направляють на
поточний ремонт. Після виконання такого ремонту у разі потреби повторюють
діагностування. З цією метою на великих АТП установлюють діагностичне
устаткування на дільниці поточного ремонту. Така організація ТО з діагностуванням
дає змогу підвищити пропускну здатність дільниці Д-1 на 30…40%, оскільки
підготовчі операції виконують на дільниці ТО-1. Істотно зменшується ймовірність
невиконання змінної програми ТО-1 через несвоєчасне усунення несправностей за
результатами діагностування. Спрощується також експлуатаційно-технічна документація
(немає потреби складати діагностичну карту Д-1).
Практика роботи АТП
показала, що перед ТО-1 діагностувати системи, від яких залежить безпека руху,
недоцільно. Значні несправності трапляються рідко. Отже, немає потреби
затрачати сили і кошти на їхній попередній пошук перед ТО-1, а регулювальні
роботи загальною трудомісткістю до 5…10 люд.-хв (залежно від потужності АТП)
можна виконати при заключному діагностуванні, використовуючи відповідні
устаткування і прилади.
Організація
діагностування Д-1 на окремому посту (дільниці) вигідно відрізняються і від ТО-1,
суміщеного з діагностуванням (на потоковій лінії). На потоковій лінії ТО-1 з Д-1
недоцільно застосовувати конвеєри, оскільки діагностування гальм на кожній осі
автомобіля порушує ритм роботи лінії, а переміщення автомобілів своїм ходом
призводить до загазованості приміщення.
Відомо також, що на
великих АТП однієї лінії ТО-1 з Д-1 не досить. Отже, треба мати кілька
комплектів діагностичного устаткування, а це економічно невигідно, бо важко
забезпечити його повне завантаження. Якщо ж розмістити один комплект
діагностичного устаткування на дільниці Д-1, то можна піднести продуктивність
праці дільниці Д-1 у 2…3 рази порівняно з потоковими лініями ТО-1 з Д-1. Крім
того, Д-1-могутній індустріальний засіб відділу технічного контролю для
перевірки якості ТО й поточного ремонту.
Перед тим як
організувати виконання ТО з діагностуванням за описаною типовою технологією,
слід на АТП залежно від конкретних умов підприємства провести відповідну
підготовчу роботу. Треба встановити й налагодити діагностичне устаткування,
укомплектувати бригади виконавців, навчити їх роботи за технологічними картами
і, перерозподіляючи операції по постах, забезпечити рівномірне завантаження
виконавців.
1.3.5 Ритм виробництва – це частина часу роботи зони ТО, яка припадає на одне обслуговування

де Т – тривалість роботи зони ТО на добу, год. Згідно з
дод. 3 [1], приймаємо Т = 16 годин (робота в дві зміни).
Підставивши числові значення, одержимо ритм виробництва для зони
ТО-2, ТО-1 та ЩО:
хв
хв
хв
1.3.6 Такт поста і лінії. Такт – це час виконання ТО на посту
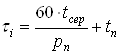
де tсер – середня трудомісткість одного ТО,
люд-год.

де Ті – сумарна річна трудомісткість і-го виду
ТО транспортних засобів (див. табл. 1.6 та 1.4), зменшена на трудомісткість
діагностичних робіт (їх виконують окремо на постах Д-1 та Д-2), люд-год;
Nі – річна кількість і-го виду технічних обслуговувань (див. табл.
1.3);
рn – кількість робітників, які одночасно працюють на посту (значення
вибираємо з додатка 4 [1]);
tn – час переміщення автомобіля при встановленні його на пост і
з’їжджанні з поста tn = 1…3 хвилини.
Для постів ТО-2:
люд-год
хв
Для постів ТО-1:
люд-год
хв
Такт лінії визначається аналогічно такту поста:
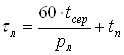
де рл – кількість робітників на лінії:

де рn – кількість робітників, які одночасно
працюють на посту (значення вибираємо з додатка 5 [1]);
Xn – кількість постів лінії, для ліній ТО-1 Xn = 2…3
пости, для ліній ТО-2 Xn = 3…5 постів
tn – час переміщення автомобіля з поста на пост:

де La – габаритна довжина автомобіля, м;
а – відстань між автомобілями на постах, м;
Vк – швидкість переміщення автомобіля конвеєром, м/хв.
Величина Vк =8…12 м/хв.
Величина а = 1,2 м для автомобілів І категорії, 1,5 м –
для ІІ та ІІІ категорії, та 2,0 м для IV категорії. В нашому випадку, а =
1,5 м.
В результаті розрахунків отримаємо:
хв.
Кількість постів лінії ТО-2 приймаємо 4, кількість виконавців на
посту лінії – по 4 робітники на посту.
Таким чином,
чоловік.
хв.
Кількість постів лінії ТО-1 приймаємо 3, кількість виконавців на
посту лінії – по 3 робітники на посту.
Таким чином,
чоловік.
хв.
1.3.7 Кількість універсальних постів ТО,
ПР, загального Д-1 та
поглибленого Д-2 діагностування, робіт розраховуємо за формулою
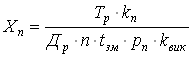
де Тр – річний об’єм робіт (див. табл. 1.6),
люд-год;
kn – коефіцієнт нерівномірності завантаження постів, приймаємо відповідно
до додатка 6 [1];
Др – кількість робочих днів за рік (приймаємо у відповідності до завдання
на КР);
n – кількість змін роботи на добу (див. дод. 3, [1]);
tзм – тривалість зміни, (див. дод. 3, [1]), год;
рn – кількість одночасно працюючих на одному посту, (приймаємо значення
не більші ніж наведено в дод. 4, [1], чол.;
kвик – коефіцієнт
використання робочого часу поста, приймаємо відповідно до дод. 7, [1].
При визначенні кількості робочих постів загального діагностування
(Д-1) підсумовуємо трудомісткості загально-діагностичних робіт ТО-1 і поточного
ремонту, а для поглибленого діагностування (Д-2) – трудомісткості робіт
поглибленого діагностування при ТО-2 і таких же робіт ПР. Якщо через малу
трудомісткість не можна спроектувати окремі пости Д-1 та Д-2, то ці
трудомісткості додаємо і розраховуємо суміщений пост діагностування Д-1+Д-2.
При розрахунках кількості постів ТО-1 та ТО-2 з обсягу сумарної
трудомісткості їх робіт необхідно обов’язково вирахувати трудомісткість
відповідних діагностичних робіт.
Розрахунок постів проводимо змінюючи у доступних межах число виконавців
робіт до отримання цілого числа постів в границях ±10%.
У разі неможливості отримати хоча б один робочий пост, споріднені
роботи можна об’єднувати і проектувати суміщені пости.
Для розрахованих даних по трудомісткостях окремих видів робіт,
кількість відповідних постів складе:
-
пости діагностування Д-1
(при kn = 1,09; рn = 2; kвик
=0,9):

-
пости діагностування Д-2
(при kn = 1,09; рn = 2; kвик
=0,9):

-
пости технічного
обслуговування ТО-1 (при kn = 1,09; рn = 2;
kвик =0,98):
Приймаємо 1 пост ТО-1.
-
пости технічного
обслуговування ТО-2 (при kn = 1,09; рn = 3;
kвик =0,98):
Приймаємо 1 пост ТО-2.
На основі отриманих даних, можна зробити висновок, що через малу
трудомісткість деяких видів робіт, виникає необхідність проектувати суміщені
пости за рахунок об’єднання трудомісткостей, а саме:
-
пости діагностування Д-1 та
Д-2:

Приймаємо 2 пости загального та поглибленого діагностування.
Таким чином, в результаті розрахунків ми отримали такі пости:
-
пости технічного
обслуговування ТО-1 – 1 пост;
-
пости технічного
обслуговування ТО-2 – 1 пост;
-
суміщений пост
діагностування Д-1 та Д-2 – 2 поста;
1.4 Розрахунок чисельності виробничого
персоналу, допоміжних робітників, ІТП і службовців
Розрізняють технологічно необхідну (явочну) Рт і
штатну Рш кількість робітників. Кількість явочних робітників
у зонах ТО і ПР визначаємо як добуток кількості робочих одного поста рп,
прийнятого при розрахунку постів, на кількість постів чи кількості виконавців
однієї лінії на кількість ліній і на кількість змін роботи зони.
Наприклад, для зони ТО-1 будемо мати:
-
зона ТО-1 (1 поста по 2
робітники на посту, 2 зміни роботи) 1·2·2 = 4 чоловік;
За результатами розрахунків складаємо табл. 1.11.
Таблиця 1.11. Результати розрахунку чисельності виробничого
персоналу
Зони,
відділення, дільниці |
Річна
трудомістк. робіт, люд-год |
Річний
фонд часу, год |
Кількість робітників |
Розподіл
по змінах |
Явочних |
Коеф.
штатності |
Штатних |
1 |
2 |
Розрахункова |
Прийнята |
1 |
2 |
3 |
4 |
5 |
6 |
7 |
8 |
9 |
Постові
роботи |
Пост
діагностування Д1+Д2 |
3572,59 |
2070 |
1,72589 |
1,73 |
0,85 |
4 |
2 |
2 |
Пости
ТО-1 |
6255,711 |
2070 |
3,02208 |
3,02 |
0,85 |
4 |
2 |
2 |
Пости
ТО-2 |
9564,345 |
2070 |
4,62046 |
4,62 |
0,85 |
6 |
3 |
3 |
Чисельність допоміжних робітників приймаємо у співвідношенні, що
вказане у додатку 10 [3]. Додатково слід передбачити для обслуговування очисних
споруд по одному робітнику на кожні 75 м3/добу витрат оборотної
води.
Нормативи витрат оборотної води приймаємо відповідно до [7] на
один автомобіль, м3/добу:
-
для легкових автомобілів 0,5;
-
для автобусів 0,68;
Витрати оборотної води для заданого АТП складуть:
м3/добу.
Розподіл чисельності допоміжних робітників за видами робіт
приймаємо у відповідності до додатку 11 [3].
Результати розрахунків зводимо в табл. 1.12.
В графі 1 таблиці 1.12 повторюються види робіт, що приведені в
додатку 11, а також робітники по обслуговуванню очисних споруд.
Таблиця 1.12. Результати розрахунків кількості допоміжних
робітників
Види
допоміжних робіт |
Співвідношення
до загальної кількості, % |
Розрахункова кількість робітників |
Прийнята
кількість робітників |
1 |
2 |
3 |
4 |
Ремонт
та обслуговування технологічного обладнання, оснастки та інструмента |
20 |
4,1 |
5 |
Ремонт
та обслуговування інженерного обладнання, сіток та комунікацій |
15 |
3,075 |
4 |
Транспортні
роботи |
10 |
2,05 |
3 |
Приймання,
зберігання та видача матеріальних цінностей |
15 |
3,075 |
4 |
Перегін
рухомого складу |
15 |
3,075 |
4 |
Прибирання
виробничих приміщень |
10 |
2,05 |
3 |
Прибирання
території |
10 |
2,05 |
3 |
Обслуговування
компресорної установки |
5 |
1,025 |
2 |
Обслуговування
очисних споруд |
- |
2,812 |
3 |
Всього |
100 |
|
31 |
1.5 Розрахунок та вибір
основного технологічного обладнання
Пости зон ТО і ПР
устатковуються канавами і підйомниками. При обслуговуванні і ремонті легкових
автомобілів в зонах передбачається 20% канав від кількості усіх постів і 40%
постів обладнуються підйомниками.
Кількість основного
обладнання визначають за ступенями його використання. Якщо воно використовується
протягом усієї зміни то його визначають за трудомісткістю, а якщо періодично – то
по табелю обладнання або даних літературних джерел [1, 3, 4, 5, 11, 12].
Обладнання загального
призначення (верстаки, інструмент) приймаємо в залежності від кількості
робітників.
Кількість обладнання:
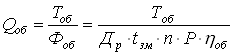
де Тоб
– річна трудомісткість певного виду робіт, люд-год;
Др – кількість робочих днів на рік;
tзм – тривалість роботи зміни, год;
n – число змін роботи (додаток 3);
С – кількість робітників, які одночасно працюють на даному виді
обладнання;
зоб – коефіцієнт використання обладнання за часом (для верстатів зоб
= 0,75…0,8 для зварювального і ковальського обладнання зоб = 0,85…0,9,
для нагрівальних печей зоб = 0,60…0,75).
Інше основне обладнання
вибирають за каталогами [1, 11] і складають відомість (табл. 1.13), до складу
якої входить все технологічне і допоміжне обладнання.
Таблиця 1.13. Відомість обладнання поста діагностики та ТО
№ |
Назва,
обладнання, шифр, марка |
Кількість |
Габаритні
розміри, мм |
Площа,
яку займає обладнання, м2
|
Потужність
електродвигунів, кВт |
|
|
одиниця |
всього |
|
1 |
2 |
3 |
4 |
5 |
6 |
7 |
|
1 |
Пульт
управління стендом |
1 |
500х500 |
0,25 |
0,25 |
0,5 |
|
2 |
Стенд
для комплексної перевірки автомобіля К-622 |
1 |
1500х2500 |
3,75 |
3,75 |
|
|
3 |
Пересувний
стенд для перевірки електрообладнання автомобілів |
1 |
500х500 |
0,25 |
0,25 |
|
|
4 |
Бак
для палива |
1 |
200х400 |
0,08 |
0,08 |
|
|
5 |
Пристрій
для заміру витрат палива |
1 |
200х400 |
0,08 |
0,08 |
|
|
6 |
Реостат
управління стендом |
1 |
1100х400 |
1,44 |
1,44 |
|
|
7 |
Стіл
діагноста |
1 |
2000х1000 |
2,0 |
2,0 |
|
|
8 |
Світлове
табло |
1 |
- |
- |
- |
|
|
9 |
Стелаж
для інструмента |
1 |
1500х400 |
0,6 |
0,6 |
|
|
10 |
Шафа
для приладів |
1 |
1400х600 |
0,84 |
0,84 |
|
|
11 |
Інструментальна
тумбочка |
1 |
400х500 |
0,2 |
0,2 |
|
|
12 |
Верстак
слюсарний |
1 |
1800х1200 |
1,96 |
1,96 |
|
|
13 |
Канавний
підйомник |
1 |
- |
- |
- |
|
|
14 |
Верстат
свердлильний настільний |
1 |
800х600 |
0,48 |
0,48 |
0,8 |
|
15 |
Рейковий
ручний прес |
1 |
800х600 |
0,48 |
0,48 |
|
|
16 |
Комплект
інструменту слюсаря ремонтника |
1 |
600х600 |
0,36 |
0,36 |
|
|
17 |
Установка
для промивання двигуна |
1 |
600х600 |
0,36 |
0,36 |
|
|
18 |
Шафа
для ручного механізованого інструменту |
1 |
1000х400 |
0,4 |
0,4 |
|
|
В результаті розрахунків ми одержали значення трудомісткості робіт
по централізованому ТО маршрутних транспортних засобів 10627,05 люд.-год, для
чого необхідно організувати на базі філії «Темп-Авто» один пост ТО суміщений з
проведенням діагностичних робіт.
2. Конструкторська частина
2.1 Класифікація різьбозгвинчуючого
обладнання
До нашого часу ще не склалась кінцева термінологія в назвах
обладнання для розбирання і збирання різьбових з’єднань (РЗ). Деякі вчені
називають його різьбовідгвинчуючим (різьборозгвинчуючим) і різьбозагвинчуючим,
інші – різьбовідверчуючим або різьбозатягуючим (різьбозаверчуючим). На наш
погляд, найбільш оптимальна назва запропонована проф. Д.Н. Решетовим – різьбозгвинчуюче
обладнання, так як цей термін поєднує як обладнання для розбирання, так і
обладнання для збирання РЗ.
Процес розбирання РЗ в багатьох випадках являється
важковиконуваним або взагалі неможливим в зв’язку з корозійним впливом
навколишнього середовища на машини, що експлуатуються. Це ускладнює
використання спеціалізованих технологічних засобів і виникає необхідність
застосування газового або електричного різання з послідуючою заміною
пошкоджених деталей.
В наш час в нових автомобілях в більшості застосовуються РЗ з
антикорозійними покриттями (гальванічними, полімерними і іншими). Це дає
можливість в більших масштабах використовувати при ремонтних
розбирально-збиральних роботах різьбозгвинчуюче обладнання з базуванням або
кантуванням об’єктів ремонту.
Розглядуване обладнання класифікується на стаціонарне (з блоковими
силовими головками) і переносне (механізований інструмент) з електричним,
пневматичним і гідравлічним приводом. Основним елементом робочих органів обладнання
являється шпиндель – вал, який передає обертання від двигуна до гайкового ключа
або головки (патрона) для утримання шпильок і гвинтів.
В зв’язку з цим по числу робочих органів і призначенню обладнання
поділяється на одно- і багатошпиндельні гайковерти, шпильковерти і гвинтоверти
[1]. На рис. 1.1. показана класифікація існуючого на даний час
різьбозгвинчуючого обладнання.
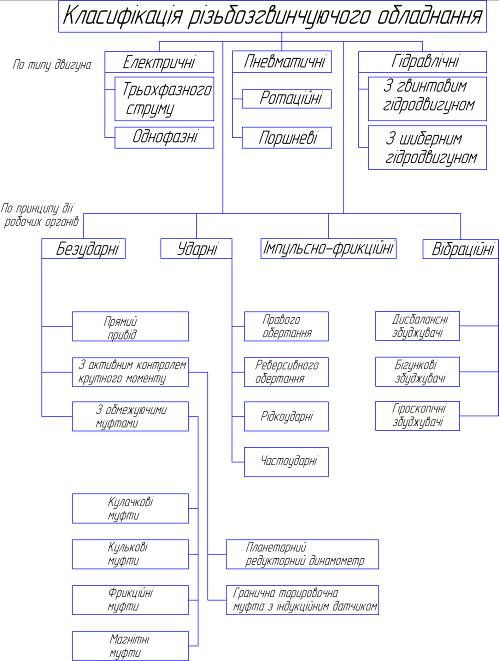
Рис. 2.1. Класифікація різьбозгвинчуючого обладнання
2.2 Багатошпиндельне різьбозгвинчуюче
обладнання
Застосування багатошпиндельного різьбозгвинчуючого обладнання
обумовлюється перш за все вимогами підвищення продуктивності праці, точності
затягування і рівномірністю розподілу навантаження на різьбові з’єднання. На
складальних операціях приміняють як підвісні багатошпиндельні установки, так і
стаціонарні багатошпиндельні різьбозгвинчуючі станки. З допомогою підвісних
установок здійснюється тільки загвинчування наживленого кріплення, а на станках
проводиться автоматична подача, наживлення і затягування кріплення. Станки
можуть вбудовуватися в автоматичні лінії або використовуватися як окреме
складальне обладнання.
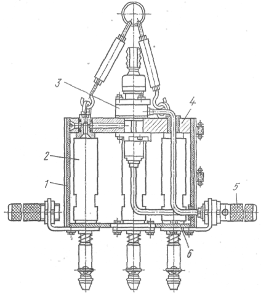
Рис. 2.2. Типова підвісна пневматична різьбозагвичуюча машина
Багатошпиндельні підвісні
різьбозагвинчуючі установки поділяють по типу приводу на пневматичні,
електричні і гідравлічні. Підвісна чотирьохшпиндельна установка для затягування
гайок складається з силових пневматичних головок 2, закріплених на передній
плиті 6. В задній плиті 4 виконані отвори для подачі стисненого повітря до
кожної головки від пускового клапана 3. Клапан керується пусковою рукояткою 5.
Ззовні головки закриті кожухом 1, який з внутрішньої сторони покритий гумою.
Відпрацьоване повітря виходить через отвір в передній плиті, закритий пористим
матеріалом.
Регулювання крутного моменту силових головок здійснюється за
рахунок зміни тиску стисненого повітря. Крім того, в задній частині силових
головок наявні дроселі, з допомогою яких можна досягти однакової кутової
швидкості шпинделів.
Розглянемо конструкцію одношвидкісного силового пневматичного шпинделя
(головки). В корпусі з фланцем змонтовані два планетарні редуктори і ротаційний
пневмодвигун. Ключові насадки чи патрони для загвинчування шпильок кріпляться
на квадратному хвостовику, який виступає із підпружиненої шліцевої втулки. Для
регулювання моменту затягування передбачений дросель. Для підготовки стисненого
повітря до роботи пневматичні багатошпиндельні установки обладнуються спеціальними
панелями, розміщеними стаціонарно неподалік від установок, на яких встановлені
регулятор тиску, вологовідділювач і маслорозпилювач.
Електричні підвісні багатошпиндельні установки компонуються на
базі електричних силових головок. Конструктивно вони виконуються так само, як і
пневматичні установки. Двигуни живляться від мережі з частотою струму 200 Гц і
напругою 36 В. В ланцюгу живлення кожного двигуна встановлене реле максимальної
сили струму, що відключає двигун при зростанні сили струму в обмотці статора в
процесі затягування. Сила струму, при якій проходить вимикання двигуна, можна
регулювати і тим самим регулювати момент затягування різьбових з’єднань. Більш
високу стабільність затягування з застосуванням струмових реле можна отримати на
податливих різьбових з’єднаннях, коли зростання моменту проходить з меншою
швидкістю.
В машинобудуванні широке застосування
знаходять двохшвидкісні електричні головки. В роз’ємний корпус вмонтовані
високочастотний асинхронний трьохфазний електродвигун з короткозамкнутим
ротором і два планетарних редуктори. На кінці водила редуктора знаходиться
кулачкова півмуфта, профіль кулачка якої виконаний у вигляді рівнобедреної
перерізаної трапеції. З півмуфтою під дією пружини зчеплена інша півмуфта,
з’єднана з шпинделем шліцами, передає шпинделю швидкі оберти від водила. Ведена
півмуфта має можливість переміщуватися в осьовому напрямку і проковзувати по
кулачках ведучої півмуфти, коли шпиндель навантажується до крутного моменту, на
який відрегульована пружина. Одночасно водило третього редуктора має торцьові
пилкоподібні зубці і є ведучою півмуфтою обгінної муфти, обертається на малих
обертах і зчіплюючись під дією пружини з веденою півмуфтою надітою на зовнішні
шліци шпинделя, передає йому малі оберти. Півмуфта переміщується в осьовому
напрямку.
Таким чином, при відсутності навантаження на шпинделі обертання з
водила другого редуктора через кулачкову муфту передається на шпиндель, і він,
обертаючись на великих обертах, загвинчує різьбове з’єднання. В момент
затягування різьбового з'єднання крутний момент на шпинделі збільшується, при
цьому кулачкова півмуфта проковзує по зубцях ведучої півмуфти, входить в
зачеплення півмуфта з півмуфтою водила і проходить подальше затягування
різьбового з’єднання на малих обертах з підвищеним крутним моментом. Коли
крутний момент досягає заданого моменту затягування реле максимального струму
вимикає електродвигун.
В деяких складальних виробництвах отримують розповсюдження
гідрогвинтові гайковерти (показаний на листі). Двигун такого гайковерта
виконаний в вигляді трьох стальних гвинтів, які приводить в рух мастило під
тиском 60–70 кгс/см2. Через редуктор обертання передається на шпиндель.
До переваг гідрогвинтових гайковертів слід віднести високий
крутний момент на одиницю маси; високий (біля 60%) ККД; менші, чим у
пневматичних інструментів, габаритні розміри; велика зносостійкість деталей в
зв’язку з їх мащенням; можливість точного регулювання крутного моменту; безшумність
в роботі; менші експлуатаційні затрати.
Гідрогвинтові гайковерти будуть в ряді випадків більш зручнішими
для вмонтовування в гайко- і гвинтозагвинчуючі агрегати автоматичних
складальних машин і ліній.
В конструкціях багатошпиндельних різьбозагвинчуючих станків, як і
в підвісних багатошпиндельних установках, багатошпиндельний блок може
компонуватися на базі таких самих пневматичних, електричних і гідравлічних
силових головок, які приміняються в підвісних установках.
Основними вузлами багатошпиндельних різьбозагвинчуючих станків
являються різьбозагвинчуючі блоки, що встановлюються на силових столах. Силові
столи забезпечують підвід в робочу зону і відвід багатошпиндельних блоків.
Керування роботою силових столів і різьбозагвинчуючих блоків здійснюється з
пульта керування.
В залежності від конструкції вузла, що
збирається, різьбозагвинчуючі блоки можуть встановлюватися на вертикальних
стійках, горизонтальних станинах, займати будь-яке просторове положення.
В багатошпиндельних станках при способі
затягування різьбових з’єднань з контролем моменту на ключі, широко
використовуються різного роду конструкції муфт граничного моменту, точність
спрацювання яких визначає точність затягування різьбових з’єднань. Муфти
граничного моменту встановлюються на приводі кожного шпинделя. Як правило, вони
застосовуються в конструкціях багатошпиндельних блоків з приводом шпинделів від
одного двигуна. На практиці широко застосовують пружинно-кулачкові муфти як
найбільш прості по конструкції. Кулачками в даній конструкції являються ролики
1 і кульки 2, що прижаті пружинами 3. При досягненні заданого моменту
затягування, кульки, стискаючи пружини, проковзують відносно роликів. При
застосуванні цих муфт втрати крутного моменту затягування складає 20–30%.
2.3 Аналіз конструкцій гайковертів
Робочі органи по принципу дії групуються на безударні, ударні,
імпульсно-фрикційні, вібраційні. Компонування робочих органів в багатошпиндельних
пристосуваннях може бути рядна, кільцева, в перпендикулярних напрямках, під
кутом і інші.
Принцип дії робочих органів різьбозгвинчуючого обладнання
безударної (статичної) дії базується на обертальному ефекті. Можна виділити три
типи таких робочих органів: прямого приводу (без обмежувальних муфт); з
обмежувальними муфтами; з активним контролем крутного моменту згвинчування.
В робочих органах першого типу використовується пневматичний
(рідше гідравлічний) привід. Обертання від пневмодвигуна через редуктор
передається безпосередньо на шпиндель. При затягуванні різьбових з’єднань
робота здійснюється як за рахунок статичного крутного моменту, що створюється
двигуном, так і за рахунок кінетичної енергії обертальних частин приводу.
Максимальний крутний момент затягування досягається при повній зупинці двигуна.
При операціях відгвинчування реалізується тільки статичний крутний момент,
величина якого пропорційна тиску стисненого повітря в мережі живлення.
Робочі органи, що входять в склад механізованого інструменту,
дозволяють проводити розбирання-збирання різьбових з’єднань з діаметром до 12 мм;
якщо вони вмонтовуються в блоки силових головок багатошпиндельних установок, то
максимальний діаметр різьб може доходити до 25 мм [1].
Різьбозгвинчуючі робочі органи безударної дії з обмежувальними муфтами,
як правило, мають електричний привід.
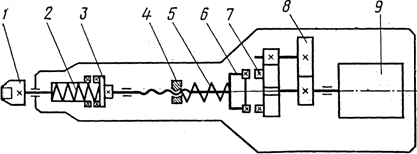
Рис. 2.4. Схема електричної силової головки: 1 – ключова
насадка; 2 – пружина; 3 – муфта вмикання; 4 – регулювальна гайка; 5 – пружина;
6,7 – складові частини кулачкові муфти; 8 – редуктор; 9 – асинхронний двигун
Крутний момент від двигуна 9 через редуктор 8 передається на муфту
з кулачками 6 і 7, виконуючу функцію обмеження ганичного моменту згвинчування.
Кулачки знаходятся в зачепленні під дією пружини 5, сила натискання якої
регулюється гайкой 4, що розміщена на вихідному валі. Муфта 3 виконує функції
вмикання і вимикання обертання ключа 1. При виконанні технологічної операції,
осьова сила, прикладена до рабочого органу, долає опір пружини 2 і муфта
вмикається, ключ починає обертатися. Після закінчення роботи дія осьової сили
припиняється, пружина 2 вимикає муфту і обертання на ключ не передається.
Крім кулачкових муфт в деяких конструкціях силових головок
використовують також кулькові, фрикційні та магнітні муфти.
В якості електричного приводу у різьбозгвинчуючого обладнання
застосовуються однофазні колекторні електродвигуни потужністю 120…750 Вт,
напругою 220 в, асинхронні електродвигуни трьохфазного і однофазного виконання
потужністю 120…750 Вт, напругою 380 і 220 в і асинхронні двигуни підвищеної
частоти 200 Гц потужністю 120…750 Вт, напругою 36 в [1].
Безударні рабочі органи з активним контролем крутного моменту
згвинчування (г= 0,08…0,15) використовуються в багатошпиндельних установках з
індивідуальним електричним (рідше пневматичним) приводом. Конструкції
контрольных пристроїв доволі разноманітні.
Найбільше розповсюдження отримали частоударні гайковерти з
гвинтовим переміщенням бойка (ударника). Вони мають електричний або
пневматичний привід і мають багато переваг у порівнянні з іншими. Продуктивність
ударних гайковертів практично задовольняє всі види виробництва (індивідуальне,
серійне, масове). В ручних машинах даного виду використовуються привідні
двигуни меншої потужності, ніж у аналогічних інструментів обертальної дії,
майже відсутній реактивний момент, що дає можливість застосовувати їх для
збирання різьбових з’єднань великих діаметрів. В наш час промисловість випускає
три типи електричних і до десяти типів пневматичних ударних гайковертів.
Рідкоударні у порівнянні з частоударними мають певні недоліки, а
саме: поява «кромочного удару» при певній жорсткості різьбових з’єднань, велика
складність конструкції ударного механізму.
Розглянемо роботу ударного механізму. При встановленні змінної
насадки на елемент РЗ, який згвинчуємо (гайка, шпилька) оператор надає робочому
органу осьове переміщення. В результаті цього долається опір зворотної пружини
і бойок, посаджений на привідний вал, своїми кулачками зчіплюється з кулачками наковальні,
яка виконана як одне ціле з шпинделем. Робоча пружина стиснення, встановлена
між упорним підшипником і бійком, кінематично замикає останній з валом з
допомогою двох кульок, які розміщені в V – подібних спіральних канавках вала і
бойка. Кульки допускають гвинтове переміщення бойка відносно вала (при
подоланні опору пружини) по одній із гілок V – подібних канавок в залежності
від напрямку обертання. В вихідному положенні бійка кульки знаходяться в
верхніх частинах канавок.
При ввімкненні двигуна бойок і наковальня обертаються як єдине
ціле і передають на шпиндель крутний момент від вала. Як тільки момент опору в
різьбовій парі перевищить момент, який створюється силою стискання пружини і
опором переміщенню кульок по канавкам, кутова швидкість наковальні і бійка
знижується, а вал продовжує обертатися з попередньою кутовою швидкістю. В цей
момент кульки починають перекочуватися по канавкам, створюючи динамічне осьове
переміщення бійка відносно вала (відскок від наковальні). При цьому кулачки
розчіплюються, а пружина додатково стискається. Обертання наковальні і шпинделя
припиняється, а бойок знову отримує кутову швидкість вала. Під дією стисненої
пружини бойку передається прискорений гвинтовий рух в зворотному напрямку і
його кулачки наносять крутний удар по кулачкам наковальні. При цьому кінетична
енергія бойка передається наковальні і через змінну насадку на згвинчуваний
елемент РЗ. Далі описаний процес періодично повторюється.
Як відомо, в якості головного параметру різьбозгвинчуємого
обладнання безударної дії приймається крутний момент згвинчування на шпинделі.
Однак при розрахунку робочих органів ударної дії цього параметру недостатньо
для обгрунтування їх техніко-експлуатаційних показників. Виникає потреба в
додатковому параметрі, який би дозволив оцінювати енергетичний баланс робочих
органів по пружним і дисипативним характеристикам складових елементів в умовах
динамічного навантаження. Таким параметром являється енергія одиничного удару.
Він легко вимірюється в виробничих умовах, а його складова – ударна потужність
(приведення енергії удару на число ударів за одиницю часу) дозволяє виконувати
об’єктивну оцінку продуктивності розглядуваних робочих органів.
На одному з листів показана одна з конструкцій пневматичних
гайковертів з ударно-імпульсною муфтою. Від пневматичного ротаційного двигуна 1
обертання передається ударно-імпульсній муфті 2 і шпинделю 3 з закріпленою на
його кінці головкою 4, що тримає гайку чи гвинт. В процесі вільного
нагвинчування гайки (або вкручування гвинта) необхідний обертальний момент
невеликий, не перевищує момент тертя в муфті, і тому швидкості обертання ротора
і шпинделя однакові. На початку затягування момент опору швидко зростає, і шпиндель
інструмента зупиняється. Однак шліцева втулка 5, яка обертається з тою ж
швидкістю, що і ротор двигуна, своїм скосом повертає кулачок 6 і виводить його
з зачеплення з шпинделем 3. При наступному обертанні з наростаючою швидкістю
механізм ударно-імпульсної муфти забезпечує зчеплення кулачка 6 з виступом на шпинделі,
що супроводжується ударом, внаслідок чого момент на головці 4 різко зростає, і
гайка (гвинт) повертається на деякий кут. Після цього кулачок знову виходить із
зачеплення, і цикл багаторазово (на протязі) повторюється з великою частотою до
повного затягування різьбового з'єднання. Таким чином, безперервне обертання
ротора двигуна перетворюється з допомогою муфти в процесі затягування в
імпульсний крутний момент на шпинделі. Цей крутний момент затягування
різьбового з'єднання значно перевищує по своїй величині момент створений
двигуном. Як показують дослідження, при збільшенні жорсткості системи, зменшенні
зазорів в зєднанні хвостовика з головкою-ключем, а також головки з гайкою
момент затягування збільшується на 50–70%.
2.4 Визначення головного параметру
різьбозгвинчуючого обладнання
Головним параметром різьбозгвинчуючого обладнання являється крутний
момент згвинчування на шпинделі Мш (крутний момент відгвинчування Мот
при розбиранні різьбових з’єднань і крутний момент затягування Мзат
при збиранні різьбових з’єднань).
Параметр Мот у об'єктів, що ремонтуються, визначається
експериментальним шляхом. В залежності від діаметру різьби, матеріалу і інших
факторів він в 1,2…2,5 рази перевищує параметр Мзат при збиранні на
заводі аналогічних нових різьбових з’єднань [1].
У нещодавно зібраних різьбових з’єднань завжди Мот<
Мзат.
Розрахункове значення Мзат для болтових і гвинтових
з’єднань визначається по формулі Біргера-Іосилевича:
,
де Q – сила затягування; d – середній діаметр різьби; h – крок
різьби; R1 и R2 – радіуси, описуючі кільцеву опорну
поверхню тертя гайки або головки гвинта; мр і мт – коефіцієнти
тертя в різьбі і на опорному торці відповідно.
Для звичайних силових метричних різьб з кутом профілю 60°
попередня формула значно спрощується:
.
Якщо елементи різьбових з’єднань виконані з одного матеріалу, то приймають:
мр=1,15 мт.
Значення Мзат для стальних болтів і гайок при
відсутності мащення визначається по формулі:
Мзат
0,2Qdн,
де dн – зовнішній діаметр різьби.
Для гвинтів з циліндричною, сферичною або шестигранною головкою
величина моменту затягування може визначатися по співвідношенню:
Мзат=0,005 dн3уT(6,5м+1),
де dн – зовнішній діаметр різьби; уT – границя
текучості матеріалу гвинта;
м – коефіцієнт тертя головки гвинта по опорній поверхні.
При визначенні Мзат для гвинтів з потайною головкою в попередній
залежності замість числового коефіцієнту 6,5 приймають 9,8 [1].
Середні значення Мот у поступивших в ремонт об’єктів і
Мзат при збиранні відремонтованих і нових об’єктів, характерні для
болтових з’єднань, приведені в табл. 2.1.
Таблиця 2.1. Середні значення моментів відгвинчування для різних
діаметрів різьби
Діаметр
різьби, мм |
6 |
8 |
10 |
12 |
14 |
Момент
відгвинчування (затягування), Нм |
15…20
(6…8) |
20…40
(14…17) |
40…80
(30…35) |
60…120
(55…65) |
100…150
(80…90)
|
Діаметр
різьби, мм |
16 |
18 |
20 |
24 |
27 |
Момент
відгвинчування (затягування), Нм |
150…200
(120–150)
|
180…300
(160–190)
|
200…350
(230–270)
|
300…450
(340–360)
|
350…500
(420–480)
|
Параметр Мзат при посадці шпильок з натягом
визначається по формулі М.П. Новікова (для метричної різьби):
Мзат =
,
де Д – ефективний (радільний) натяг по середньому діаметру різьби;
мр – коефіцієнт тертя в різьбі;
–
глибина загвинчування шпильки; dн – зовнішній діаметр різьби; Е1
і Е2 – модулі пружності 1-го і 2-го роду.
При загвинчуванні стальних шпильок із середнім діаметром різьби
10…30 мм в стальну деталь Д = 0,02…0,06, в чавунну або алюмінієву деталі –
0,04…0,12 мм [1].
Коефіцієнт мр при використанні стальної шпильки
приймається рівним 0,1… 0,2 для стальної деталі; 0,07…0,15 – для чавунної; 0,04…0,1
– для алюмінієвої або бронзової [1].
Значення модулів пружності: для стали Е1= 2,1·105;
Е2= =8,1·104 МПа; для алюмінію – Е1= 0,7·105;
Е2 = 2,7·104 МПа; для бронзи і латуні Е1
= 0,8·105; Е2 = 4,2·104 МПа [1].
Сила затягування Q знаходиться в залежності від схеми навантаження
різьбових з’єднань, міцності болта (шпильки, гвинта) і умови нерозкриття стику:
Q=кР (1-а),
де к – коефіцієнт збільшення зовнішнього навантаження (для
постійного навантаження к = 1,25…2; для перемінного – к =2,5…4,0; при
необхідності забезпечення герметичності з’єднання з плоскими металічними
прокладками к = 2,5… 3,5; те ж з м'якими прокладками – к = 1,25…2,5); Р – зовнішнє
навантаження; а = 0,2…0,4 – коефіцієнт основного навантаження, враховуючий
податливість різьбових елементів при затягуванні [1].
Слід відмітити, що до нашого часу відсутні надійні методи прямого
контролю зусиль затягування в виробничих умовах. Його фактичну величину
оцінюють лише по деяким показникам – крутному моменту затягування; куті
повороту гайки; видовженню болта і ін.
Досить складною технологічною проблемою являється затягування
групових різьбових з’єднань (безпрокладочних і особливо прокладочних). При
складанні відповідальних з’єднань важко забезпечити рівномірне затягування в кожному
болті (шпильці). В зв’язку з цим проходить нерівномірний розподіл тиску по
поверхні стику вузла, що складається, з послабленням раніше затянутих болтів,
що приводить до зниження надійності вузла.
На практиці затягування групових різьбових з’єднань проводять в
два (рідше в три-чотири) етапи. На першому етапі виконують одночасне
затягування всіх болтів (шпильок) з допомогою багатошпиндельної установки на
зусилля Q1=(0,3…0,6) Q, що забезпечує контактування стиків (Q – задана
сила затягування). На другому етапі завершують затягування шляхом послідовного
індивідуального догвинчування гайок (шпильок) до заданого крутного моменту Мзат
по оптимальних схемах, наведених на рис. 2.5.
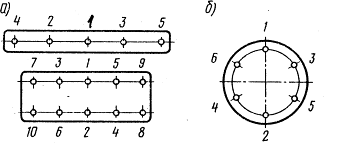
Рис. 2.5. Послідовність затягування гайок (шпильок) в
складальних одиницях: а – при стиках прямокутної форми; б – при стиках круглої
форми (цифри означають почерговість індивідуальних затягувань)
2.5 Аналіз робочого процесу і параметри
безударного різьбозгвинчуючого обладнання
Розглянемо метод визначення моменту затягування болтового
з’єднання, який створюється робочим органом прямого приводу. Цей метод
розробили проф. В.С. Корсаков і В.І. Чаннов.
Будь-яке РЗ має свою індивідуальну характеристику, обумовлену його
сумарною податливістю і силами тертя в різьбовій парі і по торцю гайки. Такою
характеристикою являється коефіцієнт кутової жорсткості РЗ: Кр=ДМ/Дц.
Цей коефіцієнт показує, на яку величину змінюється крутний момент,
який прикладається до гайки, при повороті її на кут Дц.
Кут повороту гайки являється кутом гальмування шпинделя. Чим
меньший кут гальмування (тобто більше значення Кр), тим значиміша складова
моменту затягування, що створюється кінетичною енергією обертових мас приводу.
Друга складова моменту затягування залежить від статичного
крутного моменту, який створюється пневмодвигуном. Ця с складова не являється
постійною величиною. Її максимальне значенння Мст досягається при
зупинці шпинделя (числова величина приводиться в технічній характеристиці
двигуна).
В загальному випадку робота, що затрачається на затягування Азат,
складається з двох складових: роботи Аз.д., здійснюваної за рахунок
динаміки приводу, і роботи Аз.ст, здійснюваної за рахунок статичного
моменту двигуна. Вираз для цих робіт має такий вигляд:
Аз.д.=
Аз.ст=
,
де Мш – розрахунковий крутний момент згвинчування на шпинделі
(ключі); Мст – максимальний статичний момент; цзат – кут
повороту гайки при затягуванні.
Частина енергії (Ау.д.) витрачається на пружну деформацію
елементів приводу:
Ау.д.=
де цпр – приведений кут скручування елементів приводу.
Робота на подоланння сил тертя в редукторі приводу буде рівна:
Атр.=ктр(Аз.д.+Ау.д.),
де – ктр =1-з - коефіцієнт втрат на тертя в
редукторі; з – ККД редуктора.
Знайдемо кінетичну енергію обертових мас:
,
де Іпр – момент інерції обертових мас, приведений до шпинделя;
щ0 – кутова швидкість шпинделя на холостому ході при
вільному нагвинчуванні гайки.
На основі закону збереження механічної енергії можемо записати:
.
Кут повороту цзат і кут скручування цпр
замінимо відповідними виразами:
;
,
де кпр – коефіцієнт кутової жорсткості приводу.
Підставляючи отримані залежності отримаємо розрахункову формулу:
=
.
Визначимо момент згвинчування на ключі при затягуванні болтового
з’єднання з різьбою М18 пневматичною силовою головкою (тиск стисненого повітря
в магістралі 0,5 МПа). Вихідні дані для розрахунку: Мст = 80,5 Нм; щ0=28,5с-1;
Iпр = 0,1687 кг.м2; кпр = 280 Нм; кр
= 280 Нм; ктр = 0,15. Числове значення Мш, отримане з
допомогою попереднього виразу, рівне 175 Нм, що дуже близько до значення рекомендованого
моменту затягування [1].
Для оцінки точності затягування РЗ різьбозгвинчуючим робочим
органом використовується коефіцієнт відносної нерівномірності затягування:
,
де Мш.max; Мш.min; Мш.ср – відповідно
максимальне, мінімальне і середнє значення моменту згвинчування на шпинделі при
затягуванні однотипних РЗ.
В робочих органах прямого приводу г = 0,2…0,35 [1]. Якщо
розсіювання значень моменту Мш обмежене, то необхідно зменшити вплив
динаміки приводу. Це досягається шляхом зменшення моменту інерції обертових мас
(зазвичай ротора двигуна), а також зменшенням коефіцієнта кпр (наприклад,
введенням торсіона).
Так як в розглядуваних робочих органах при згвинчуванні РЗ
виникають значні реактивні моменти, то їх доцільно використовувати переважно в
багатошпиндельних пристроях, де ці моменти взаємно зрівноважуються.
Техніко-економічні показники пневматичного різьбозгвинчуючого
обладнання статичної дії в значній мірі визначається характеристиками силового
приводу, який включає пневмодвигун (ПД) і трансмісію.
В наш час проектування ротаційних багатокамерних ПД проводиться в
основному макетно-експериментальним методом, використовуючи досвід попередніх
розробок. Однак більше число врахованих при цьому конструктивних і термодинамічних
параметрів затрудняє пошук емпіричним шляхом оптимального рішення. Традиційні
методи розрахунку, основані на індикаторних діаграмах, в даному випадку виявились
непридатними.
В.А. Чернов і Т.А. Лавриненко вирішили ряд проектних
задач шляхом математичного моделювання на ЕОМ.
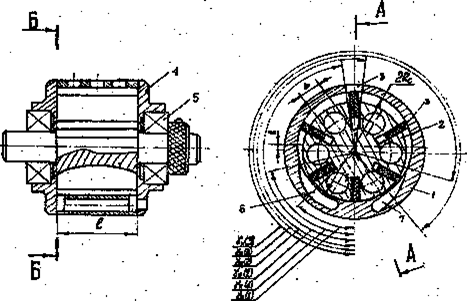
Рис. 2.6. Розрахункова схема реверсивного ротаційного ПД
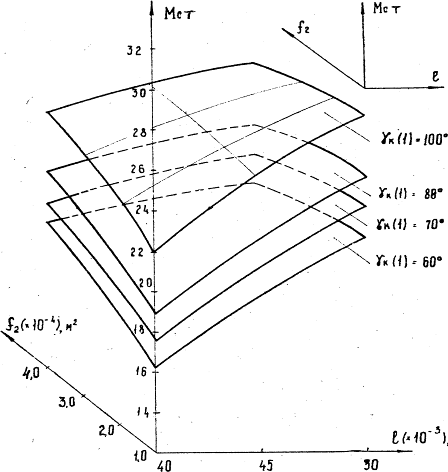
Рис. 2.7. Залежність
статичного крутного моменту загальмованого ПД від його основних конструктивних
параметрів
В корпусі статора 1 розміщений ротор 2, вісь обертання якого
зміщена на ексцентриситет е. В пазах ротора розміщені пластини (лопатки) 3, які
під дією відцентрових сил прижимаються до внутрішньої поверхні статора. Кожна
пара суміжних лопаток разом з ділянками бокових поверхонь ротора і статора,
розміщеними між ними, створює робочу камеру змінного об’єму. З торців ці камери
обмежені кришками 4, в яких розміщені підшипники ротора 5. Стиснене повітря
поступає в робочі камери через вхідне вікно 6, а видаляється в загальному
випадку через вихлопні вікна 7 і 8. Ротаційний ПД може бути реверсивним і
нереверсивним. Зміна напрямку обертання ротора в реверсивному ПД здійснюється
зміною функцій впускного і випускного каналів. Для того, щоб забезпечити однакові
робочі характеристики ПД при різних напрямках обертання ротора, впускні і
випускні вікна повинні бути розміщені симетрично відносно осі симетрії.
Характерною особливістю реверсивних ПД являється наявність
центрального випускного вікна, яке забезпечує попередій випуск повітря із
робочої камери з метою зменшення від’ємної роботи по стисненню повітря при куті
повороту ротора більше 180 °.
При математичному моделюванні враховувались слідуючі конструктивні
параметри ПД: Rc – внутрішній радіус статора;
– довжина камери; гн
(1) і гк (1) – кути початку і кінця випуску повітря через вікно 6; гн
(2) и гк (2) – кути початку і кінця центрального вихлопу через вікно
8; гн (3) и гк (3) – кути початку і кінця випуску повітря
через вікно 7; f2 - площа центрального вихлопного отвору. В якості
основних були вибрані такі параметри: Rc;
; f2; гн(1);
гк(1); гн (2).
За критерій якості ПД приймався статичний крутний момент Мст
(Нм) загальмованого ПД.
Із графіків слідує, що точка, що відповідає максимальному значенню
Мст, визначається оптимальними значеннями конструктивних параметрів
ПД: Rc= 24 мм;
= 50 мм;
f2=1 см2; гн(1)= 40°; гк(1)=
100°; гн(2) = 175°. При цьому дотримані умови геометричної симетрії
реверсивного ПД:
гн(1)+ гк(3)=2р;
гк(1)+ гн(3)=2р;
гн(2)+ гк(2)=2р.
Найбільший вплив на Мст має кут початку центрального
вихлопу, довжина камери (ротора) і площа вихлопного вікна.
Для передачі обертання від високообертових роторів ПД до шпинделя
робочого органу використовуються понижуючі планетарні передачі типу 2К – Н (рис. 2.8).
Знайдемо формулу для розрахунку передаточного відношення даного
планетарного механізму, для цього скористаємось методом зупинки водила (методом
Вілліса). Планетарному механізму надається обертання з кутовою швидкістю,
рівною кутовій швидкості водила з протилежним знаком.
Відносний рух ланок при цьому залишається таким, яким він був до
зупинки водила. Таким чином, після надання всім ланкам кутової швидкості водила
з від’ємним знаком планетарна передача перетворюється в просту, зв’язок між кутовими
швидкостями якої можна легко знайти з допомогою відомих залежностей.
Складемо рівняння, що зв’язують кутові швидкості
, основних ланок
планетарної передачі 2К-Н, де а, b і Н – це відповідні ланки 1, 3 і Н (в нашому
випадку
=0).
Нехай
– кутові
швидкості основних ланок a, b і Н. Після надання планетарному механізму
додаткового обертання з кутовою швидкістю водила з від’ємним знаком, тобто
після того, як додали до
величину
–
ланки будуть мати кутові
швидкості:
;
;

При непорушному водилі зв’язок між кутовими швидкостями
і
такий самий, як між
абсолютними кутовими швидкостями в простій передачі, тобто:

Для планетарної передачі типу 2К-Н маємо:
,
і відповідно,
.
Якщо, наприклад, відомо, що
,
то з попередньо отриманої формули будемо мати:
.
На основі цієї формули отримаємо:
.
Число зубів коліс передачі вибирається таким чином, щоб
виконувались наступні умови:
– співосності Z1+ 2Z2= Z3;
– складання (Z1+ Z3)/C=ціле число;
– сусідства Z2+2<(Z1+ Z3)
sin (р/C),
де С – число сателітів.
В результаті спільного рішення даних рівнянь знаходять Z1,
Z2, Z3.
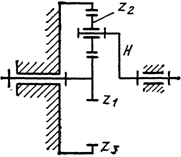
Рис. 2.8. Схема планетарної передачі типу 2К-Н
Передачі 2К-Н мають постійний момент на виході, добре забезпечують
реверс, мають мінімальну віброактивність. Оптимальний діапазон передаточних
відношень і1Н=2,7…8 при ККД 0,96…0,98 [1].
2.6 Розрахунок планетарної передачі
Спеціального методу розрахунку планетарних передач на міцність ще
нема. Розрахунок ведеться по тим самим методам, що і простих передач, але з
врахуванням особливостей планетарних передач.
На вихідному валу гайковерта потрібно мати момент, рівний 60Нм=6
, для затягування різьб
М10. Число обертів вихідного вала за хвилину
об/хв.
Термін експлуатації гайковерта – 2000 годин.
Гайковерт реверсивний, працює в постійному режимі.
1. Визначення передаточного числа і характеристики планетарного
ряду k. Приймемо число обертів пневмодвигуна рівне 1360 об/хв і визначимо
передаточне відношення планетарної передачі:
.
Виразимо передаточне відношення через величину
з основного рівняння кінематики:
, але
;
;
.
2. Визначення коефіцієнта корисної дії.
;
;
.
Це видно і з виразу передаточного відношення
, де з збільшенням
збільшується
.Отже х= +1, тоді прийнявши
([3] с. 131),
отримаємо:
.
Це означає, що ККД планетарної передачі
вище ККД простої передачі з тим самим числом полюсів, хоча передаточне число
планетарної передачі на одиницю більше.
3. Визначення споживаної потужності:

4. Визначаємо число зубів коліс.
а) Розглядаємо менше зубчасте колесо.
З умови співосності:
маємо
, поділивши на
отримаємо:
.
Якщо k>3, як в нашому випадку, то меншим колесом буде сонячне.
б) Число зубів сонячного колеса визначимо з умов складання:
;
,
де С – число сателітів.
При будь-якому числі
, що
кратне 5, отримаємо ціле число зубів, але це число не повинно бути менше
мінімального числа зубів по умовах непідрізання і бути недопустимо більшим по
умовам виготовлення і збереження мінімальних габаритів. Крім того, це число
повинно забезпечувати ціле число зубів сателітів, яке отримаємо з умов
співосності при незмінному значенні k.
Приймаючи послідовно значення
,
рівні 30, 35, 40, 45, 50, отримаємо
рівне
18, 21, 24, 27, 30. Але числа зубів
рівні
21 і 27 не забезпечують цілого числа зубів сателітів:
.
Таким чином, залишаються числа зубів сонячного колеса, рівні 18,
24, 30, 36, 42.
в) Числа зубів на інших колесах:
72 (96, 120, 144, 168);
27 (36, 45, 54, 63).
5. Визначення моментів.
а) Момент на ведучому валу:
.
б) Момент на веденому валу:
.
в) Момент на епіциклічному колесі:
, або
.
Далі потрібно визначити найбільш навантажений полюс, але для
розглядуваної схеми, коли зусилля в полюсах рівні, зрозуміло, що при однакових
матеріалах в гірших умовах знаходиться сонячне колесо, так як число зубів його
менше, а число циклів навантажень більше. Хоча зуби сателітів в такій схемі
планетарного механізму працюють на згин з знакоперемінними навантаженнями
навіть при постійному напрямку обертання, так як в зачепленні з сонячним і
епіциклічним колесами зуб працює різними сторонами, але реверс гайковерта
згладжує цю особливість роботи сателітів.
6. Відносні числа обертів.
Сонячне колесо:
об/хв.
Епіцикл:
об/хв.
Сателіт:
об/хв.
7. Визначення міжосьової відстані коліс.
Міжосьова відстань коліс планетарної передачі визначається з умови
витривалості по контактним напругам при зупиненому водилі, тобто так само, як і
для простої передачі.
Ця відстань може бути визначена в залежності від обертового
зусилля, крутного моменту, або потужності.
Вихідною являється формула Герца-Бєляєва:
,
де
– зусилля, що
припадає на одиницю довжини контакту;
– приведений модуль першого роду;
– приведений радіус кривизни в точці контакту.
Величини цих параметрів визначаються з умов:
,
де
– розрахункова
обертова сила, момент і потужність;
([3] с. 134), так як обидва колеса виготовлені з сталі;
,
де
– радіуси
шестерні і колеса;
– кут зачеплення;
– ширина колеса.
Підставляючи в вихідну формулу і розв’язуючи відносно міжосьової
відстані
, отримаємо:
,
де
.
Будемо рахувати по моменту на сонячному колесі:
,
де
– відповідно
коефіцієнти динамічності і концентрації навантаження;
– коефіцієнт, який враховує нерівномірність розподілу
навантаження між сателітами.
Приймаємо для фланкірованих зубів
([3]
с. 135).
При симетричному розміщенні колеса відносно опор
([3] с. 135).
При плаваючих центральних колесах
([3]
с. 135).
Тоді отримаємо:

Допустима контактна напруга залежить в основному від поверхневої
твердості матеріалу, його термічної обробки і потрібного терміну придатності
передачі. Крім того, залежить від в'язкості мастила, степені точності
виготовлення і чистоти поверхні:
.
Матеріал колеса – сталь 40Х з твердістю RC=45ч50. Колесо
виготовлене по 7-й степені точності ГОСТ 1643–56 з чистотою робочої поверхні
зуба по сьомому класу ГОСТ 2789–59.
– коефіцієнт, який залежить від твердості поверхні зуба,
матеріалу і його термічної обробки.
При RC=50
=190ч240 ([3] с. 136).
Приймаємо
=240.
– коефіцієнт, що враховує в'язкість мастила, визначається
графічним методом. В нашому випадку кінетична в'язкість в cct при температурі
мастила, що надходить в зачеплення, лежить в межах
,
то
([3] с. 136).
– коефіцієнт, який залежить від завершальних операцій. При 10
класі чистоти
([3] с. 136).
– число циклів, що відповідає тривалій межі витривалості. Для
сталі 40Х з твердістю RC=50
([3] с. 136).
– число циклів, що обчислюється за формулою:
.
При реверсивному редукторі з однаковою ймовірністю роботи в обидві
сторони загальний час роботи ділиться на 2.
Так як
, то приймаємо
.
Тоді отримаємо:
.
Коефіцієнт ширини колеса
ч
([3] с. 136) найбільш
широко розповсюджений для планетарних передач. Приймаємо
.
Міжосьова відстань буде рівна:
.
8. Діаметр сонячного колеса

Для планетарних передач міжосьова відстань не являється основним
параметром, який визначає габарити редуктора. Тому діаметр розрахункового
колеса можна визначати відразу.
З отриманої вище формули
,
і враховуючи що
і
,
отримаємо:
або
.
Приймаючи ширину колеса
, де
– коефіцієнт ширини колеса
отримаємо:
.
В нашому випадку при
,
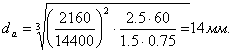
9. Модуль зачеплення.
При
, 
,
або
.
При
,
,
.
Приймаємо модуль зачеплення
,
при
,
.
Тоді
і 
10. Перевірка зубів на згин.
Визначаємо напруження згину
.
Напруження стискання
.
Сумарне напруження
,
де
– обертова сила;
– крок;
– кут тиску при вершині зубів;
– коефіцієнт форми зуба, визначається з виразу
і
.
Рівняння міцності
,
де
– розрахункова
обертова сила;
– коефіцієнт, що враховує вплив перекриття.
Напруження зуба рівне:
.
Замінюючи
,
і
,
отримаємо
.
Звідки

.
Наближено коефіцієнт форми зуба можна визначити по емпіричній
формулі, яка має вигляд:
.
Для внутрішнього зачеплення, виконаного з 7-ою ступінню точності,
можна орієнтовно прийняти
([3] с. 139).
Допустиме нормальне напруження від згину при реверсивній передачі
обчислюється за формулою:
;
ч
,
і так як
, то приймається
, де
– межа витривалості зразка
на згин при симетричному циклі навантаження;
– ефективний коефіцієнт концентрації напружень біля основи зуба
ч
([3] с. 139), в
залежності від матеріалу, радіусів скруглень і їх обробки.
Проте в нашому випадку якість сталі 40Х покращена і твердість її
становить RC=50, то при цьому допустиме контактне напруження не рахується, а
воно рівне 9000ч10000
.
Напруження згину, що сприймається зубом
.
Таким чином зуб має надлишкову міцність при згинанні
.
Можна було б ще зменшити модуль зачеплення, але це приведе до дуже
великої кількості зубів, а дуже малі розміри сателіта мішають компактному
розміщенню підшипників.
Отже, остаточно приймаємо:
,
,
;
;
;
Для перевірки прийнятого значення коефіцієнта динамічності
навантаження визначають обертову швидкість в полюсі зачеплення при відносному
русі:
.
11. Особливості розрахунку осей сателітів.
Розрахункова схема осі сателіта залежить від жорсткості зв’язку її
обох опор. В нашому випадку ці опори жорстко зв’язані між собою в суцільному
водилі і вісь сателіта розраховується на згин як балка, що лежить на двох
опорах.
Навантаження на вісь і опори, як це слідує з умови рівноваги
сателіта, рівна
.
Розрахункова обертова сила, прикладена до сателіта, в полюсах
зачеплення без врахувань втрат на тертя
.
.
Внаслідок рівності обертових сил в полюсах зачеплення сателіта з
сонячною шестернею і епіциклом будуть рівні і радіальні сили в цих полюсах,
. Ці сили зрівноважаться на
сателіті. Отже, сила, що згинає вісь сателіта і навантажує підшипники,
.
Але при числах обертів, що наближаються до тисячі, необхідно вже
враховувати відцентрову силу, що діє в радіальному напрямку і згинає вісь
сателіта, а також навантажує підшипник. Ця сила рівна:
,
де
– вага деталей,
відцентрова сила яких навантажує вісь сателіта і її опори (сателіт, підшипники,
частина осі сателіта, яка не має опори, розпірні втулки);
– так званий радіус водила, тобто відстань від центральної осі до
осей сателітів;
– кутова швидкість обертання водила в 1/с.
Для зменшення величини відцентрової сили потрібно намагатися
зменшити вагу сателіта і деталей його опори, до зменшення кутової швидкості
водила і його радіуса. В нашому випадку
.
Таким чином, на основі аналізу конструкцій різьбозгвинчуючого
обладнання та існуючих методик його розрахунку ми провели розрахунок
планетарної передачі гайковерта, який може бути використаний при виконанні
операцій по ТО і ремонту на станціях технічного обслуговування.
3. Технологічна частина
3.1 Способи оцінки зміни технічного
стану автомобілів та їх агрегатів
Визначення технічного стану автомобілів та
агрегатів особливо необхідно, коли вузол або агрегат відмовив. По окремим
практично встановленим ознакам можна знайти спряження або вузол, де порушена працездатність.
Але це крайній випадок. Бажано момент настання відмови передбачати заздалегідь
для того, щоб його виключити.
У практичних умовах вузол (агрегат) ремонтують, деталі заміняють
на основі наявного досвіду експлуатації автомобілів у заданих умовах, пробіг до
ремонту оцінюють по статистичним даним з великою погрішністю. Підвищення
точності оцінки технічного стану агрегату дозволяє зменшити витрати на ремонт
несправного агрегату за рахунок прогнозування пробігу автомобіля до настання
граничної зміни технічного стану, якщо відомі гранична величина, закономірність
зміни критерію в процесі експлуатації і стан вузла (агрегату) за попередній
пробіг.
Причиною зміни технічного стану вузла є знос. Але, визначають
безпосередньо по зносу тільки технічний стан шин, коробки передач, заднього
моста, рульового керування – по зміні висоти протектора, по зазорах у зубчастих
передачах, у шарнірах і інших спряженнях. Величину несправності вузлів,
агрегатів оцінюють по зміні експлуатаційних показників: витраті масла, проривові
газів у картер двигуна, шумам, температурі нагрівання й ін.
При обґрунтуванні оптимального режиму технічного обслуговування
автомобіля перелік операцій визначають за коефіцієнтом повторюваності,
періодичність установлюють поки що по статистичним даним пробігуу автомобіля до
припустимого значення параметра вузла, агрегату. Оскільки пробіг до граничного
стану вузла є випадковим, то розкид даних великий і тому для зниження витрат
періодичність до технічного обслуговування приймають більше мінімальної, з
урахуванням довірчого рівня імовірності. Але при цьому, як відомо, визначена
частина автомобілів має потребу в технічному обслуговуванні раніш установленої
періодичності, а більша частина – пізніше. Для скорочення витрат на технічне
обслуговування і підвищення надійності необхідно проводити робити, коли
параметр досягає припустимого значення. А це важливо тільки при своєчасному і
точному визначенні технічного стану автомобіля без його розбирання. Технічний
контроль, що у даний час в автотранспортних підприємствах роблять головним
чином візуально, недостатньо ефективний, оцінка технічного стану залежить від
кваліфікації контролера. Для об'єктивного контролю необхідні відповідні
контрольні прилади. Інструментальне визначення технічного стану вузла, агрегату
без розбирання називають діагностикою.
У залежності від технології проведення діагностику поділяють на
стендову і ходову, застосовують головним чином стендову. Для ходової
діагностики на автомобіль установлюють прилади на час випробувань, наприклад,
мірний бачок при перевірці витрати палива автомобілем. Більш прогресивної є
ходова діагностика за допомогою вбудованих приладів, що дозволяють у будь-який
момент перевірити стан агрегату (за прикладом покажчика температури води, тиску
масла і кількості палива в баці).
Застосування засобів діагностики знижує витрати на технічне
обслуговування і поточний ремонт на 5%, витрата запасних деталей і матеріалів –
на 10%, палива і шин – на 20%. Строк окупності засобів діагностики у великому
(500–600 автомобілів) автотранспортному підприємстві біля року.
Для створення приладів, за допомогою яких можна визначити
технічний стан агрегату без розбирання, необхідно, насамперед, установити
діагностуючий симптом, що характеризував би технічний стан об'єкта, зміну в
структурі об'єкта.
Технічний стан автомобіля характеризують структурні параметри
(зазори, міжцентрові відстані, прогини, зсуви, лінійні розміри, стан поверхонь
деталей, що сполучаються, і т.д.). Взаємодія автомобіля з зовнішнім середовищем
(дорожні, кліматичні й ін. умови) змінюють його технічний стан. Зміна
структурних параметрів агрегатів автомобіля має визначені закономірності, не
вивчені в повному обсязі.
При роботі складних динамічних систем відбуваються різного роду
фізичні, механічні, хімічні й інші процеси. Параметри цих процесів називають
вихідними, вони змінюються зі зміною структурних параметрів. Вихідні процеси
залежать від зовнішніх умов, технічного стану об'єкта (внутрішніх умов). При
діагностуванні приймають зовнішні умови строго фіксованими, і тоді зміна вихідних
процесів визначається тільки зміною структурних параметрів об'єкта.
Про зміну технічного стану вузла можна судити по безпосередній
ознаці (наприклад, розбраковування деталей за результатами їхніх вимірів); по
сукупності непрямих ознак (наприклад, оцінка стану газорозподільного механізму
по стуках і вібраціях). При відомому чіткому взаємозв'язку структурних і
вихідних параметрів об'єкта у визначених умовах останні можна приймати за
непрямі ознаки або симптоми несправного технічного стану вузла (агрегату) без
його розбирання, тому що вихідні процеси і відповідні їм вихідні параметри
можна спостерігати і вимірювати ззовні. Щоб параметр вихідного процесу міг
стати діагностичним симптомом, він повинний бути однозначним, зі строгою
залежністю структурного параметра і параметра вихідного процесу; із широким
полем зміни, коли відносна зміна параметра вихідного процесу набагато більше
зміни структурного параметра; зручним для виміру.
Діагностичні симптоми по ступені їхньої взаємозалежності поділяють
на незалежні і залежні. Незалежні вказують на конкретну несправність (виміром
величини прогину труби карданного вала безпосередньо визначають несправність).
Ці симптоми ще називають частковими, вони вказують на цілком конкретну
несправність вузла або механізму. Наприклад, знос гальмових накладок колеса
визначають по гальмовому шляху колеса або гальмовому зусиллю на цьому колесі і
по величині вільного ходу педалі. Визначити знос накладок тільки по величині
гальмового шляху неможливо. До складу симптомів комплексних входять часто
загальні, що характеризують технічний стан об'єкта в цілому, наприклад,
величина потужності двигуна, витрата палива, сумарний окружний люфт деталей
трансмісії, загальний рівень шуму агрегату, величина гальмового шляху, тиску
масла в магістралі й ін.
Необхідні глибокі дослідження несправних станів вузлів і агрегатів
автомобіля і супутніх їм вихідних процесів і їхніх параметрів, що могли б
служити симптомами несправностей. Для цього варто вивчити характерні процеси,
що супроводжують роботу спряження, що знаходиться в справному або несправному
станах (шум, вібрація, стукіт, коливання тиску й ін.), виконати аналіз
параметрів цих процесів з погляду відповідності вимогам до діагностичних
симптомів, досліджувати закономірності зміни параметрів, що супроводжують
вихідні процеси від пробігу вузла або агрегату, установити припустимі і
граничні значення цих параметрів для різних умов експлуатації, розробити
ефективні методи і швидкодіючу апаратуру для фіксації діагностичних симптомів.
При оптимальному діагностуванні будь-яку несправність об'єкта діагностики можна
знайти по найменшому числу симптомів, отже, застосовувати мала кількість
приладів і датчиків і звести до мінімуму трудомісткість діагностування,
досліджувати і розробити точні методи прогнозування з метою встановлення
ресурсу безвідмовної роботи вузла, агрегату, автомобіля в цілому.
Як діагностуючі симптоми застосовують різні параметри, у тому
числі:
-
величину відносного зсуву
сполучених деталей (окружні люфти в агрегатах трансмісії, зазори між торцями
коромисла або штовхальника і клапана, між шворнем і втулкою, у підшипниках
коліс, пробуксовка зчеплення);
-
швидкість і температуру
нагрівання сполучень (якість регулювання підшипників вала, гальм і ін.);
-
герметичність робочих
об’ємів (тиск у шинах, витік повітря з камери згоряння двигуна, течі,
підтікання й ін.);
-
вміст домішок в маслі, склад
і концентрацію компонентів у відпрацьованих газах двигуна;
-
потужнісні, економічні
показники і т.д.
Перед виміром перерахованих параметрів оцінку технічного стану
вузла, агрегату роблять візуальним контролем. Упровадження технічної
діагностики, інструментальної перевірки не заміняє операції технічного
контролю, суб'єктивної оцінки стану механізму при перевірці виконання обсягу і
якості технічного обслуговування і поточного ремонту.
При діагностиці складних механізмів необхідно спочатку виміряти
параметри, що характеризують агрегат у цілому, а потім переходити до
діагностики елементів механізму. Зміна технічного стану вузла, агрегату
автомобіля попередньо можна оцінити в кількісній формі на основі системного
підходу до автомобіля, по зносі, наприклад, протектора шин, зубчастих передач,
шлицевих з'єднань, хрестовин і т.д.
При діагностиці двигуна оцінюють його працездатність по мощностним
і економічних показниках. З цією метою вимірюють силу тяги або потужність,
витрата палива при заданому навантаженні і швидкості руху. Потужність можна
виміряти по інтенсивності розгону автомобіля при повному відкритті дроселя.
Про технічний стан автомобіля судять і по величині механічних
втрат в агрегатах трансмісії, за результатами зовнішнього огляду. Чим більше
механічні втрати, тим менше накат. Накат автомобіля визначають по шляху,
пройденому автомобілем з поставленим у нейтральне положення на швидкості 30 км/год
важелем коробки передач. На стенді за допомогою електродвигуна можна вимірити і
коефіцієнт корисної дії трансмісії автомобіля. При нейтральному положенні
важеля коробки передач включають електродвигуни навантажувального пристрою
стенда і вимірюють величину моменту, що крутить, необхідного для привода
трансмісії.
3.2
Прогнозування пробігу автомобіля до технічного обслуговування і ПР його
агрегатів
Прогнозування потреби якого-небудь агрегату в ремонті дозволяє ще
до настання відмови виконати регулювальні роботи, підготувати деталі для
поточного ремонту і виконати поточний ремонт при оптимальному пробігу.
Прогнозувати потреба агрегату в поточному ремонті можна по економічному або
технічному критеріях, а також по зміні технічного стану даного агрегату.
Прогнозуванням технічного стану спряження називають науково
обґрунтоване визначення з відомою імовірністю пробігу, після закінчення якого
діагностичний параметр або експлуатаційний показник досягне заданого значення.
Для прогнозування зміни технічного стану вузла або агрегату необхідно знати
закономірність зміни критерію стану в залежності від пробігу автомобіля і
результати діагностування при різних пробігах конкретного вузла або агрегату.
Оскільки причиною зміни технічного стану вузлів автомобіля є знос
сполучень, те і прогнозувати варто був б знос сполучень. Практично таке
прогнозування можливе для шин і тих вузлів, у яких вимір зазору в сполученнях
можна виконати порівняно просто і з високою точністю. Зазор, люфт у сполученнях
досить просто можна вимірити в системі керування, наприклад, кермового колеса,
у редукторі заднього моста, між зубами шестірень коробки передач, у карданних
шарнірах, у шліцевих з'єднаннях і т.д.
Прогнозування зносу спряжень і деталей у процесі експлуатації
автомобіля можна робити по зносі шин, (рис. 3.1), де приведені дані по
зносі протектора шини автомобіля в залежності від пробігу. Глибина канавки
нового протектора 10 мм; після пробігу 5,5 тис км. вона стала 8,8 мм,
знос склав 1,2 мм. При такій інтенсивності зношування протектора пробіг
автомобіля до повного його зносу складе значно більше 40 тис. км – крива 1. За
результатами другого виміру можна скорегувати пробіг автомобіля до зняття
покришки в ремонт для накладення нового протектора (крива 2), він трохи менше
40 тис. км. Помилка прогнозування величини пробігу шини до граничного стану
може бути через те, що прийнято лінійну залежність замість експонентної.
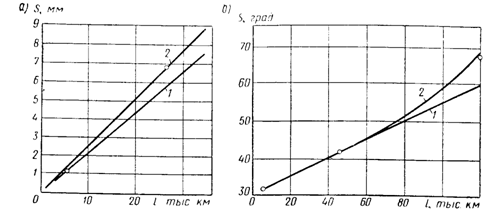
Рис. 3.1. Зміна технічного стану вузлів
у процесі експлуатації автомобіля: а – знос S протектора шипи автомобіля у
залежності від пробігу l за результатами двох вимірів: 1 – першого; 2 – другого;
б – зміна зазору (люфту) S у редукторі автомобіля у залежності від пробігу l: 1
– лінійна залежність; 2 – експонентна залежність
Приведений графічний спосіб прогнозування є найпростішим, його
цілком можна застосовувати при лінійній закономірності зносу або зміни іншого
критерію технічного стану вузла в залежності від пробігу автомобіля. Аналогічно
можна прогнозувати знос гальмових накладок.
Знос інших спряжень деталей, зміна більшості експлуатаційних
показників має більш складну закономірність.
Прогнозувати технічний стан деяких агрегатів, вузлів і спряжень
можна тільки за експлуатаційними показниками, тому що виміряти зазори, люфти
без розбирання вузла неможливо. Так, технічний стан сполучення кільце – канавка
поршня двигуна внутрішнього згоряння можна оцінити по витраті масла на угар,
сполучення кільце – гільза – по витоку газу в картер, підшипників колінчатого
вала і всієї сукупності сполучень двигуна внутрішнього згоряння, змащення яких
проводиться під тиском, по зміні тиску в системі мащення.
Прогнозування потреби агрегату в поточному ремонті варто робити
головним чином за економічним критерієм. Заміну агрегату, вузла, деталі роблять
при мінімальних сумарних питомих витратах Са на придбання і на
підтримку Спр працездатності:
Питомі витрати на придбання Са залежать від вартості
агрегату Са і його пробігу l після установки:
Питомі витрати на підтримку працездатності Спр залежать
від вартості
СД замінних детальний, вузлів, величини заробітної
плати Сз робітником за установку, збитку Сп від простою автомобіля і
пробігу l з початку експлуатації:
При розрахунку питомих витрат на підтримку працездатності при
пробігу l автомобіля з початку експлуатації підсумовують вартість усіх
замінених за цей час деталей, зарплату робітників за установку всіх цих деталей
і збитки від простою автомобіля при заміні деталей, що відмовили, або вузлів.
По питомих витратах визначають економічно обґрунтований пробіг автомобіля до
заміни дорогої деталі, вузла, агрегату і постановки автомобіля в капітальний
ремонт.
3.3 Планово-попереджувальна система технічного обслуговування і
ремонту рухомого складу
Для підтримки рухомого складу автомобільного транспорту в технічно
справному стані, необхідному для нормальної експлуатації, прийнята
планово-попереджувальна система технічного обслуговування і ремонту.
Технічно справний стан рухомого складу досягається шляхом
технічного обслуговування і ремонту.
Технічне обслуговування проводиться примусово в плановому порядку через визначені пробіги
або час простою рухомого складу.
Ремонт призначений для відновлення і підтримки працездатності рухомого
складу, усунення відмов і несправностей, що виникли при роботі або виявлених у
процесі технічного обслуговування. Ремонтні роботи виконуються як по потребі
(після появи відповідної відмови або несправності), так і за планом через
визначений пробіг або час роботи рухомого складу – попереджувальний ремонт.
Технічне обслуговування і ремонт рухомого складу роблять з
попереднім контролем або без нього. Основним методом проведення контрольних
робіт є діагностика, що служить для визначення технічного стану автомобіля й
агрегатів без розбирання.
Ціль діагностики при технічному обслуговуванні полягає у
визначенні дійсної потреби в проведенні робіт, виконуваних при кожному
обслуговуванні, і прогнозуванні моменту виникнення відмови або несправності.
Види
технічного обслуговування і ремонту
Технічне обслуговування рухомого складу по періодичності,
перелікові і трудомісткості виконуваних робіт поділяється на:
Ø
щоденне технічне
обслуговування (ЩО);
Ø
перше технічне
обслуговування (ТО-1);
Ø
друге технічне
обслуговування (ТО-2);
Ø
сезонне технічне
обслуговування (СО).
Щоденне обслуговування (ЩО) містить у собі: перевірку прибуваючих
з лінії і рухомого складу, що випускається на лінію, зовнішній догляд за ним і
заправні операції. Для перевірки рухомого складу в автотранспортному
підприємстві створюється контрольно-технічний пункт (КТП) з оглядовою канавою і
комплектом необхідних інструментів, пристосувань і устаткування.
При перевірці рухомого
складу, що прибуває з лінії, установлюються: час прибуття, покази спідометра і
залишок палива в баці автомобіля; комплектність рухомого складу; наявність
несправностей, поломок, ушкоджень; потреба в поточному ремонті.
При випуску на лінію рухомого складу перевіряється його зовнішній
вигляд, комплектність і технічний стан, а також виконання призначеного для
нього напередодні обслуговування або ремонту (за даними зовнішнього огляду й
облікової документації).
Перевірка проводиться по визначеному переліку операцій, що
складається в автотранспортному підприємстві з урахуванням конструкції
використовуваного рухомого складу й умов його експлуатації. Перелік повинний
передбачати обов'язкову перевірку справності систем, агрегатів, вузлів і
деталей рухомого складу, що впливають на безпеку руху, у тому числі рульового
керування, гальм, підвіски, коліс і шин, кабіни, приладів зовнішнього
освітлення, світлової і звукової сигналізації, склоочисників.
Для виконання операцій зовнішнього догляду за рухомим складом, що
полягають у прибиранні кабіни, мийці.
Заправні операції ЩО – заправлення автомобілів паливом,
доливання масла в картер двигуна й охолодної рідини в радіатор роблять водії за
рахунок свого робочого часу, передбаченого режимом їхньої роботи. Заправлення
паливом проводиться, як правило, на автозаправних станціях по талонах,
доливання масла і води в автотранспортному підприємстві.
Терміни проведення ЩО обумовлюються пробігом рухомого складу за
робочий день.
Перше технічне обслуговування (ТО-1) включає контрольні,
кріпильні, регулювальні і мастильні операції, виконувані, як правило, без
зняття з рухомого складу або часткового розбирання (розкриття) приладів, що
обслуговуються, вузлів і механізмів.
ТО-1 виконується протягом проміжку часу між робочими змінами
рухомого складу (у міжзмінний час).
Друге технічне обслуговування (ТО-2) містить у собі всі операції
ТО-1, що проводяться в розширеному обсязі, причому в разі потреби прилади, що
обслуговуються, вузли і механізми розкривають або знімають з рухомого складу.
Для проведення ТО-2 рухомий склад може зніматися з експлуатації.
Технічне обслуговування ТО-1 і ТО-2 виконується через визначений
пробіг, встановлюваний у залежності від умов експлуатації рухомого складу.
Сезонне технічне обслуговування (СО) проводиться 2 рази в рік.
Воно є підготовкою рухомого складу до експлуатації в холодний і теплий час
року, переважно сполучається з ТО-2 з відповідним збільшенням трудомісткості
робіт.
У кожному автотранспортному підприємстві повинні складатися
щомісячні плани-графіки виконання ТО-1 і ТО-2, що враховують періодичність
проведення цих видів обслуговування і планові середньодобові пробіги рухомого
складу. Терміни постановки рухомого складу в обслуговування можуть вказуватися
в планах-графіках або загальному пробігу від початку експлуатації за
показниками спідометра, або календарними днями. При користуванні
планами-графіками другого типу вони підлягають поточному коректуванню по
фактичному пробігу рухомого складу.
3.4 Регламентні роботи по ТО маршрутних
транспортних засобів
Перелік регламентних робіт по технічному обслуговуванню
транспортних засобів при досягненні визначеного пробігу або по кількості
місяців експлуатації наведено в табл. 3.1–3.2.
Технічні характеристики мікроавтобусів Mercedes Benz 207D – 410D,
які використовуються в якості маршрутних ТЗ для перевезень пасажирів, та
величини заправних об’ємів технічних рідин наведені в табл. 3.3.
Таблиця 3.1. Регламентні роботи (заміна масла та фільтрів) по
технічному обслуговуванню транспортних засобів
|
тис. км |
10 |
20 |
30 |
40 |
50 |
60 |
70 |
80 |
90 |
100 |
К-ть місяців |
Заміна масла в
двигуні |
В НУ |
* |
* |
* |
* |
* |
* |
* |
* |
* |
* |
Кожні 12 |
В ТУ |
* |
* |
* |
* |
* |
* |
* |
* |
* |
* |
Кожні 6 |
Заміна масляного
фільтра |
В НУ |
|
* |
|
* |
|
* |
|
* |
|
* |
Кожні 12 |
В ТУ |
* |
* |
* |
* |
* |
* |
* |
* |
* |
* |
Кожні 6 |
Таблиця 3.2. Регламентні роботи (діагностичні та регулювальні) по
технічному обслуговуванню транспортних засобів
|
тис. км |
20 |
40 |
60 |
80 |
100 |
120 |
140 |
160 |
180 |
200 |
|
місяці |
12 |
24 |
36 |
48 |
60 |
72 |
84 |
96 |
108 |
120 |
Заміна фільтруючого
елемента повітряочисника |
Через кожні 20 тис.
км |
Перевірка теплових
зазорів в клапанному механізмі |
Через кожні 40 тис.
км |
Заміна паливного
фільтра |
|
* |
|
* |
|
* |
|
* |
|
* |
Заміна паса
газорозподільчого механізму, перевірка стану насоса системи охолодження |
|
|
|
|
* |
|
|
|
|
* |
|
тис. км |
20 |
40 |
60 |
80 |
100 |
120 |
140 |
160 |
180 |
200 |
|
місяці |
12 |
24 |
36 |
48 |
60 |
72 |
84 |
96 |
108 |
120 |
Перевірка стану і
регулювання натягу пасів приводу допоміжних агрегатів |
|
* |
|
* |
|
* |
|
* |
|
* |
Перевірити частоту
холостого ходу двигуна |
|
|
|
|
|
* |
|
|
|
|
Заміна охолоджуючої
рідини в системі охолодження двигуна |
Перший раз через
200 тис. км або 120 місяців, далі через кожні 100 тис. км або 60 місяців |
Заміна робочої
рідини в трансмісії |
МКП |
В нормальних умовах |
|
|
|
|
|
* |
|
|
|
|
В тяжких умовах |
|
|
* |
|
|
* |
|
|
* |
|
АКП |
В нормальних умовах |
|
|
|
|
|
* |
|
|
|
|
В тяжких умовах |
|
|
|
* |
|
* |
|
* |
|
* |
Перевірка стану
передніх і задніх гальмівних механізмів |
Через кожні 10000 км
або 6 місяців |
Заміна гальмівної
рідини |
Через кожні 36
місяців |
Перевірка стану, а
при необхідності регулювання стоянкового гальма |
* |
* |
|
* |
|
* |
|
* |
|
* |
Виконати
перестановку коліс (перевірка стану шин та тиску в них проводиться щомісячно) |
Через кожні 10000 км |
Візуальний
контроль
|
Шарніри рульових
тяг, рульовий механізм, захисні чохли шарнірів та рульового механізмів
Деталі та вузли
підвіски
Захисні чохли
шарнірів півосей
|
Через кожні 10000 км
або 6 місяців |
|
тис. км |
20 |
40 |
60 |
80 |
100 |
120 |
140 |
160 |
180 |
200 |
|
місяці |
12 |
24 |
36 |
48 |
60 |
72 |
84 |
96 |
108 |
120 |
Гальмівні шланги та
магістралі
Рівень та стан всіх
робочих рідин
Система випуску
вдпрацьованих газів
Паливопроводи та їх
з’єднання
|
* |
* |
* |
* |
* |
* |
* |
* |
* |
* |
Таблиця 3.3. Технічні характеристики мікроавтобусів Mercedes Benz
207D – 410D, та величини заправних об’ємів технічних рідин
|
MB 208D, 308D,
408D
|
MB
210D, 310D, 410D
|
MB
207D |
MB
207D, 307D, 407D |
Двигун |
601.940 |
602.940 |
616.917 |
616.934 |
Кількість циліндрів |
4 |
5 |
4 |
Робочий об’єм |
2299 куб. см |
2874 куб. см |
2404 куб. см |
Максимальна потужність |
Механічна трансмісія |
Автоматична трансмісія |
Механічна трансмісія |
Автоматична трансмісія |
Механічна трансмісія |
58 кВт (78 к.с.) при 3800 об/хв |
60 кВт (81 к.с.) при 4000 об/хв |
70 кВт (95 к.с.) при 3800 об/хв |
72 кВт (98 к.с.) при 4000 об/хв |
48 кВт (65 к.с.) при 4200 об/хв |
Максимальний крутний момент |
157 Нм при 2000–2800 об/хв |
192 Нм при 2400–2600 об/хв |
|
Об’єм масла в картері двигуна |
6.5 л |
7.0 л |
6.5 л |
Об’єм заповнення системи охолодження |
7.0 л |
7.5 л |
11.7 л |
Трансмісія
|
Механічна |
Автоматична |
Механічна |
Автоматична |
Механічна |
Механічна |
Об’єм масла в коробці передач |
2.3 л |
5.9 л |
2.3 л |
5.9 л |
2.3 л |
2.3 л |
Тип масла |
SAE 80W-90 |
ATF |
SAE 80W-90 |
ATF |
SAE 80W-90 |
SAE 80W-90 |
Об’єм масла в гідропідсилювачі та його тип |
1.6 л, ATF |
Об’єм масла в картері заднього моста та його тип |
1.8 л, 85W – 90 |
3.5 Рекомендації по застосуванню
паливо-мастильних матеріалів і спеціальних рідин закордонного виробництва при
технічному обслуговуванні
Таблиця 3.4. Еквіваленти мастильних матеріалів і спеціальних рідин
закордонного виробництва
Продукт
вітчизняного виробництва |
Відповідний закордонний сорт продукту |
|
British Petroleum |
Castrol |
Esso |
Mobil |
Shell |
Teboil |
Agip |
|
|
Олії моторні
М-10М2К ДСТ 8581–78
|
ВР Vanellus |
Castrol CRB 30 HD |
Essolube 5DX*SAE 20W/30 |
Mobil Delvac 1230 |
Shell Rotella SX oil |
Teboil HPO |
Agip F.I. Diesel Camma |
|
М-8М2К ДСТ 8581–78
|
ВР Vanellus |
Castrol CRB 20 HD |
Essolube 5DX* SAE 20W/30 |
Mobil Delvac 1220 |
Shell Rotella SX oil SAE 20W/20 |
Teboil HPO SAE 20W/30 |
Agip F.I Diesel Camma SAE 20W/30 |
|
М-6з/10В (ДВ-АСЗ-10У) |
ВР Super Viscostatic SAE 10W/40 |
Castrolite 10W/30HD* |
Esso extra motor oil SAE 10W/30 |
Mobil Special SAE 10W/30 |
Shell X – 100 SAE 10W/30 |
Teboil Silver Low cash super motor oil SAE 10W/30 |
Agip F.I. Super Motor oil Multi-grade 10W/40 |
|
М-10ДМ |
Vanellus oil MS-3 30; Energol Diesel S-3 30 |
Agricastrol HDD 30 |
Standard HD-3 30; Essolube DX-3 30 |
Mobil oil Universal 30; Mobil Delvac 1330 |
Rimula CT30 |
– |
F-l Diesel Sigma 30 |
|
М-8ДМ |
– |
– |
– |
Mobil Delvac 1320 |
Rimula CT20W |
– |
– |
|
ТСп-15ДО ДСТ 23652–79 |
BP Gear oil EP SAE 90 |
Castrol ST90 |
Esso Gear oil EP90 |
Mobillube HD |
Shell Spirax 90 EP |
Teboil Hipoid SAE 80W/90 |
– |
|
Тап-15В ДСТ 23652–79 |
BP Gear oil EP SAE 90 |
Castrol ST90 |
Esso Gear oil EP90 |
Mobillube З 90 |
Shell Spirax 90 EP |
– |
Agip F. 1. Rotra |
|
ТСп-10 ДСТ 23652–79 |
BP Muiti Gear oil 80/90 EP |
Castrol SCL (80 EP) |
Esso Gear oil CP 80 |
Mobillube CX SAE 80 |
Shell Spirax 80 EP |
– |
Agip F.I. Rotra |
|
Масло для гідросистем автомобіля марки «Р» |
BP ATF Type A, Suffix A |
Castrol TQ Type A, Suffix A |
Esso Torque Fluid 40 |
Mobilfluid 93, Mobil DTE 11 |
Shell Tellus Т 23 |
Teboil Fluid A |
BP Energol HL50 |
|
Амортиза-торна рідина АЖ-12Т
ДСТ 23008–78
|
BP Aero Hydraulic 2 |
Castrolaero Fluid 8528 |
Aviation utillity oil, DEF 2901 A |
– |
Aeroshell Fluid 1 |
Tebo
hidraulic oil 55
|
– |
|
Гідравлічне масло МГЕ-10А |
BP Aero Hydraulic 1 |
Castrolaero 585 В Grade 1 |
Univis J-43 |
Mobil HPA |
Aeroshell Fluid 41 |
– |
– |
|
Масло веретенне АУ ДСТ 1642–75 |
BP Energol HL50 |
– |
Esso Univis 40 |
Mobil Avrex 903 Mobilfluid 93 |
Aeroshell Fluid 7; Shell Vitrea 21 |
– |
– |
|
Масло гидравлічне АУП |
– |
Castrolaero fluid 5575; |
Univis PJ-42 |
Mobilfluid 93 |
Aeroshell Fluid 7; Shell Tellus 21 |
– |
– |
|
Автомобіль-на гальмова рідина ГТЖ-22М |
Pentosin Super Fluid J 1703-R |
Castrol Hyspin P Castrol Girling Brake Fluid
(Green)
|
Atlas Brake Fluid CD |
Mobil Hydraulic Brake Fluid |
Shell Donax У |
– |
Agip F-l Brake Fluid Super HD |
|
Гальмівна рідина «Нева» |
Energol Brake Ruid |
– |
– |
Mobil Hydraulic Brake Fluid 550 |
– |
Jarruneste Teb – Brake |
– |
|
Антифриз ТОСОЛ-А40 |
– |
– |
– |
– |
– |
– |
Fi
Antifreese SAE 78R3
|
|
Охолоджуюча низькозамерзаюча рідина марки 40 ДСТ 159–52 |
– |
– |
– |
– |
– |
– |
– |
|
Спирт етиловий технічний ДСТ 18300–72 |
– |
– |
– |
– |
– |
– |
– |
|
Литол-24 ДСТ 21150–75 |
Energrease L2 Multipurpose; Energrease LS3 |
Spheerol AP3;
Castrolease LM
|
Beacon 3 Unirex 3; Essoroller 2 |
Mobilgrease 22; Mobilgrease BRB; Mobillux 3 |
Retinax A Atvania 3 R3; Alvania RA; Gyprina 3; Caprina RA |
Teboil Universal EP |
– |
|
Мастило №158 |
Energrease L2 Multipurpose; Energrease LS3 |
– |
Beacon 2 |
Mobilgrease Special and MP |
Retinax A |
Teboil Universal M |
– |
|
Солідол синтетичний С ДСТ 4366–76 |
Energrease C2, C3; Energrease GP2, GP3; Energrease PR2, PR3 |
Helveum 2, 3; Spheerol L Gastrolease WP; Impervia GS |
Chasuis XX; Cazar K2; Estan 2 |
Mobilgrease AAN2 Greasrex D 60; Gargoyle У N2 |
Unedo 2; 3; Livona 3; Blameta 2, 3 |
– |
– |
|
Прес-солідол синтетичний С ДСТ 4366–76 |
Energrease C1, CA; Energrease GP1 |
Castrolease CL; Helveum 1; Castrolease Т |
Chassis L, H;
Cazar Kl;
Estan 1; Maroleum 1
|
Mobilgrease AAN 1 |
Unedo 1; Blameta 1; Retinax З |
– |
– |
|
Солідол жировий Ж ДСТ 1033–79 |
Energrease C2, C3; Energrease GP2, GP3; |
Helveum 2, 3; Spheerol L Castrolease WP Impervia GS |
Chassis XX; Cazar K2; Estan 2 |
Mobilgrease AAN2 Greasrex D60; Gargoyle У N2 |
Unedo 2 3; Livona 3; Blameta
2, 3
|
– |
– |
|
Прес-солідол жировий Ж ДСТ 1033–79 |
Energrease PR2, PR3 Energrease C1, CA;
Energrease GP1
|
Helveum 1; Castirolease CL;
Castrolease Т
|
Chassis L, H; Cazar Kl; Estan 1; Maroleum 1 |
Mobilgrease AANI |
Unedo L Blameta Retinax З |
– |
– |
|
Мастило графітне УСсА ДСТ 3333–80 |
Energrease C2G, C36; Energrease GP 2-G, GP3-G |
Helveum 2 Graphited; Spheerol LG Castrolease Graphited |
Van Estan 2 |
Graphited
№3
|
Barbateia
2, 3, 4
|
– |
– |
|
Мастило жирове 1–13 |
Energrease N2, N3; Energrease RBB2, RBB3; Energrease HTS |
Spheerol S; Spheerol HS Castrolease CS; Castrolease WB; Impervia
MM2, MM3 |
Andok M 275; Andok B; Andok 260 |
Mobilgrease BRB №3; Mobilgrease BRB Lifetime |
Nerita 2, 3; Retinax H; Albida 2, 3 |
– |
– |
|
Мастило ЦИАТИМ-201 ДСТ 6267–74 |
– |
– |
Beacon 325 |
Mobilgrease BRB Zero |
Aeroshell Grease 6 |
– |
– |
|
Мастило ЦИАТИМ-221 ДСТ 9433–80 |
– |
– |
– |
Mobilgrease 24** |
Aeroshell 15**, Aeroshell ISA |
– |
– |
|
Таблиця 3.5. Еквіваленти пального, мастильних матеріалів і
спеціальних рідин, виготовлених у країнах Східної Європи
|
Продукт
вітчизняного виробництва |
Індекс |
Відповідний закордонний сорт продукту |
|
Німеччина |
Чехія / Словаччина |
Польща |
Угорщина |
Румунія |
Болгарія |
СФРЮ |
|
Палива
|
|
Паливо дизельне літнє ДСТ 305–82 Л – 0,2–40, Л – 0,5–40 |
Т-161 |
DK-1 TGL
4938
|
Сорт NM-30
V
CSN 65 6506
|
IZ-50/DZ TWT-RNJe-
2/75; ILS, PN-67/C-96048; IZ-20, PN-67/C-86048
|
Gasolaj konnyu MSZ 1627–74 |
Дизельне паливо-5, дизельне паливо- 1 5 STAS 240–66 |
Сорт А,
отн-178–66
|
|
|
Паливо дизельне зимове ДСТ 305–82 3–02 мінус 35 °С, 3–05
мінус 35 °С, 3–02 мінус 45 °С, 3–05 мінус 45 °С |
Т – 160 |
Sonder-Dieselkraft-stoff** M-11061; DK-3* TGL 4938 |
Сорт
NM-30**
V
CSN
65 6506
NM-45
V
CSN 65 6506
|
IZ-50/DZ DZ-K-30*
2/75; IZ-35, PN-67/C. 96048 IZ-50 PN-67/C 96048
|
|
Дизельне паливо-35 STAS 240–66 Дизельне паливо-45 NID 3535–66 |
|
|
|
Моторні масла та технічні рідини
|
|
М-10М2К ДСТ 8581–78 М-8М2К ДСТ 8581–78,
|
|
MD-302 TGL
21148/07
|
M6 ADS 11 PND23–112–68 |
Superol CC SAE 30
PN-74/C-96048
Superol CC SAE 10W/30
PN-74/C-96088
|
DS-2–60 MF 11–74 OKGT;
ЕМД-13***
DS-2–40 MF 11–74 OKGT
|
– |
– |
Calax Super (S-3) Jus В.Н.З. 169 Tip «D» |
|
Масло трансмісійне для коробок передач ТСп-15ДО ДСТ 23652–79 |
|
Schmierol GL 125 TGL 21160 |
PP7,
V
CSN 65 6641
|
Hipol 15, PN/G-96100 u ZN-64/ MPCh/ NF-86 |
C-90, MSZ 13239/2–73 |
Т-90 ЕР-2 STAS 8960/71 |
Улита 90, БДС
9797–72
|
Hipol SAE 80. SAE 90 JUS B.H3. 302 Tip Mp-4 |
|
Масла трансмісійні для ведучих мостів ТСп-15ДО, ТАп-15В ДСТ
23652–79 |
|
Schmierol CL 125, TGL 21 160 |
Olej auto-mobilovy prevodovy PP90, TPD 23–119–72 |
Hipol 15, PN/C-96100 u ZN-64/ MPCh/
NF-86
|
Hy-k-90 MSZ 13239/41–73 |
Т-90 ЕР-2 Special NID
3805–70
|
Улита 90, ЕР, БДС
9797–72
|
Hipol SAE 80. SAE 90 JUS B.H3. 302 Tip Mp-4 |
|
Масла для гідросистем автомобіля марки «Р» |
|
Hidro 20/75–40 HLP20 |
Olej travanlivy H 3, PND 23–107–73 |
Boxol-26 BN-73/ 0635–35 |
Hidrofluid A, Termeks-zam: 55–33–93 |
|
|
|
|
Амортизаторна рідина АЖ-12Т ДСТ 23008–78 |
|
|
|
Olej do amortyza-torow Norma BN-70/0536–24 (від мінус 40 до плюс
130 °С) |
Lokharito-olaj MSZ 13238 (до мінус 25 °C) |
|
|
|
|
Охолоджуюча низькозамерзаюча рідина марки 40 ДСТ 159–52 |
|
Glysantin TGL 13665 |
EG-40A PND 31–609–72 |
Plin do chtodnic samocho-dowych PN-60/C-40006 |
Antifriz 40 MSZ 924 |
Охолодна рідина STAS 8671–70 |
|
|
|
Антифриз ТО-СОЛ-А40 |
|
' |
" |
Borygo ZN-68/ MPCh/ ТІ 1302 |
|
" |
~ |
|
|
Мастило Литол-24 ДСТ 21150–75 |
|
SWA 532, TGL 14819/0 3; SAA531, TGL 31171 |
T-SP 2–3, PND 25–026–69 |
LT-43, PN-72/C-96134 (до мінус 20 °C) LT-453 |
IZS-3, MSZ
11710/4–761; Liton З 12/11, NIMSZ 60009–72; IZS-2, MSZ 11710/4–761
|
UM 175 LiGa3, STAS 8789–71 |
|
|
Солідол синтетичний С ДСТ 4366–76 |
|
Maschinen-fett MR-2, MR-3, TGL
17746
|
T-K3, CSN 65 6911; T-Al, CSN 65 6946 |
LT-12, PN-
72/C-96134; STP, PN 63/ C-96129; Maszynowy 2, PN 68/ C96130
|
KZS-2, MSZ 11710/2–76T |
U85 СаЗ STAS 562–71; RUL 100 СаЗ, STAS
1608–72
|
Машинна ДО-2БДС 1415–72; Машинна ДО-3 БДС 1415–72 |
|
|
Прес-солідол синтетичний С ДСТ 4366–76 |
|
SWA512, TGL
14819/03
|
T-N1. CSN 65 6916 |
Maszynowy 2, PN 68/ C96130; STP, PN 63/ C-96129 |
KZS-0/1, MSZ 11710/ 2–76T |
U75 Ca2, U80 Ca, STAS 562–71 |
Авто-1 БДС
8637–71
|
|
|
Солідол жировий Ж ДСТ 1033–79 |
|
Maschinen-fett MR-2, MR-3 TGL
17746
|
T-K3, CSN 65 6911; T-
AL, CSN 65 6946
|
Maszynowy 2, PN-68/C-96130; LT-12, PN-72/ C-96134 |
KZS-2, MSZ 11710/2–76T |
U85, СаЗ, STAS 562–71; RUL 100 СаЗ, STAS 1608–72 |
|
|
|
Прес-солідол жировий Ж ДСТ 1033–79 |
|
SWA 512, TGL 14819/03 |
T-N1, CSN 65 6916 |
Maszynowy 2, PN 68/ C96130; |
KZS-0/1, MSZ 11710/ 2–76T |
U75 Ca2, USOCaO, STAS 562–71 |
Авто-1 БДС
8637–71
|
|
|
|
Змащення графітна УСсА, ДСТ 3333–80 |
|
Federnfett FF |
T-G3, CSN 65 6912 |
Grafitowany, PN-59/C-96153; Swar |
KZS-3G, MSZ 11710/ 2–76T |
Grafitate pentru D, NID 3308–64 |
Графітна, БДС
6743–67
|
|
|
Мастило жирове 1–13 |
|
SWA 532, TGL 14819/03 |
T-PH2, CSN 65 6918; T-AV2, CSN 65 6946 |
LT 1–13,
PN-58/C-96125; LT-23 PN-72/C-96134
|
NSZ-2, MSZ 11710/3–76T |
RULS
140NaCa3, STAS 1608–72
|
1–13 Вірила; Висококапна «3», БДС 1414–60 КН-230, ВІН 118/66 |
|
|
Мастило ЦИА-ТИМ-201 ДСТ 6267–74 |
|
SWD 712, TGL 14819/04 |
|
LMP, PN-
63/C-96151
|
|
U 170 Li 2, STAS
8961–71
|
|
|
|
|
|
|
|
|
|
|
|
|
|
|
|
|
|
|
|
|
3.6 Технологія діагностичних та
регулювальних робіт по рульовому керуванню
3.6.1 Система рульового
керування. Принцип дії
Обертання рульового
колеса за допомогою вала рульової колонки передається до рульового механізму.
Рульовий механізм типу «рейка-шестерня» перетворить цей обертальний рух у
прямолінійний поступальний (у поперечному напрямку) рух. Цей рух, у свою чергу,
за допомогою поперечних рульових тяг і наконечників рульових тяг передається до
поворотних кулаків.
Насос підсилювача
рульового керування подає гідравлічну рідину під тиском до рульового механізму.
У міру того як повертається рульове колесо, гідравлічна рідина проходить через
клапан рульового механізму до однієї зі сторін поршня двосторонньої дії.
Сторона, до якої подається робоча рідина, залежить від напрямку, у якому
повертається рульове колесо. Робоча рідина переміщає поршень, що є частиною рульового
механізму, забезпечуючи підсилення, необхідне для створення зусилля, необхідного
для повороту рульового колеса.
Таблиця
3.6.
Специфікації
Робоча
рідина для підсилювача рульового керування |
ATF |
Об’єм
робочої рідини в системі гідропідсилювача, л |
1,6 |
Регулювальні
параметри
|
Номінальне
значення |
Допуск |
Опорна
втулка рульового механізму, мм |
|
Втулка
поряд із блоком клапанів рульового механізму |
5,83 |
±
0,5 |
Втулка,
розташована далі від блоку клапанів рульового механізму |
4,5 |
±
0,5 |
Зусилля
провертання, Нм |
|
Виміряне
на внутрішньому ободі рульового колеса на спиці з рульовим колесом діаметром
367 мм |
35 |
±
7 |
Люфт
рульового колеса, мм |
|
Виміряний
на ободі рульового колеса |
0 –
6 |
Регулювання
рульового колеса, градуси |
|
Максимально
допустимий вільний хід (люфт) рульового колеса |
|
±
3 |
3.6.2 Огляд і перевірка
1. Візуально огляньте на
наявність очевидних ознак механічних чи електричних ушкоджень.
Таблиця 3.7. Таблиця
візуального огляду
Механічні
фактори |
Електричні
фактори |
– Тиск
у шинах
– Пас
приводу аксесуарів
– Колеса
і шини
– Протікання
робочої рідини в магістралях підсилювача рульового керування
|
– Реле
тиску підсилювача рульового керування (PSP) |
2. Якщо причина
візуально не очевидна, перевірте ознаку несправності.
Таблиця 3.8. Таблиця ознак несправності
Можливі
причини
|
Технічні
дії |
Дуже
утруднена / дуже легка дія рульового керування |
Ослаблення
чи знос паса приводу аксесуарів |
Перевірте
пас приводу аксесуарів. |
Забруднення/
звуження перерізу шланга підсилювача рульового керування |
Перевірте
шланги на наявність ушкоджень, чи перекручування, звуження прохідного
перерізу. При необхідності встановіть нові елементи |
Забруднення
робочої рідини |
ПРОМИЙТЕ
систему підсилювача рульового керування |
Аерація
(насичення повітрям) робочої рідини |
ВИДАЛІТЬ
повітря з системи підсилювача рульового керування |
Заїдання
кульових шарнірів підвіски |
Виконайте
перевірку кульових шарнірів підвіски |
Знос
рульового механізму |
Установіть
новий рульовий механізм |
Знос
рульової колонки |
|
Знос
насоса підсилювача рульового керування |
Установіть
новий насос підсилювача рульового керування |
Рульове
керування не реагує на збільшення кута повороту рульового колеса |
Знос
наконечників рульових тяг |
Перевірте
і при необхідності установіть нові елементи |
Знос
втулок передньої підвіски |
При
необхідності встановіть нові втулки |
Знос
кульових шарнірів підвіски |
Виконайте
перевірку кульових шарнірів підвіски |
Знос
верхньої опори стійки у зборі з пружиною |
Встановіть
нову верхню опору стійки в зборі з пружиною |
Знос
опорних втулок рульового механізму |
Перевірте
і при необхідності встановіть нові елементи |
Ослаблення
затягування болтів рульового механізму |
Перевірте
і при необхідності встановіть нові болти |
Ослаблення
затягування болтів кріплення рульової колонки |
Перевірте
і при необхідності встановіть нові болти |
Ослаблення
затягування болта кріплення рульової колонки до шестірні рульового механізму |
ПЕРЕВІРТЕ
і при необхідності встановіть новий болт |
Підвищений
бічний зазор у рульовому механізмі |
Встановіть
новий рульовий механізм |
Коефіцієнт
підсилення не змінюється при зміні швидкості автомобіля |
Реле
PSP або еоектрична мережа |
|
3.6.3 Перевірка
елементів. Рульовий привод
Огляньте чохли
рульового механізму на наявність порізів, зсуву, скручування чи деформації.
Переконаєтеся в
надійності закріплення чохлів. При необхідності встановіть нові чохли чи
хомути.
1. Встановіть
автомобіль на сухій, рівній, горизонтальній поверхні і задійте стоянкове
гальмо. Зцентруйте рульове керування (положення «прямо вперед»).
2. При працюючому
двигуні акуратно поверніть рульове колесо вправо і вліво, щоб перевірити люфт.
Люфт вимірюється на ободі рульового колеса і його величина повинна знаходитися
в межах, встановлених специфікацією. Якщо величина люфту виходить за
встановлені межі, визначить: чи зношено рульовий привод, рульова колонка чи
наявний підвищений бічний зазор у рульовому механізмі.
3. Якщо рульовий привод
зношений, при необхідності встановіть нові елементи. Рульова колонка ремонту не
підлягає. Встановіть нову колонку. Бічний зазор рульового механізму регулюванню
не підлягає. Встановіть новий рульовий механізм.
4. При виключеному
двигуні візьміться за рульове колесо і міцно тримайте його двома руками.
Спробуйте перемістити рульове колесо вниз, а також вліво – вправо, при цьому не
обертаючи його. Це дозволяє перевірити знос підшипників рульової колонки, зазор
у шарнірі вала рульової колонки і послаблення в рульовому колесі чи колонці.
При виявленні люфту перевірте правильність затягування болтів рульової колонки,
муфти вала колонки і рульового колеса.
3.6.4 Промивання системи
гідропідсилювача рульового керування
1. Від’єднайте
розширювальний бачок системи охолодження від колісної арки.
1. Викрутіть болт.
2. Від’єднайте
розширювальний бачок системи охолодження.
3.Використовуючи
придатну заглушку, заглушіть бачок підсилювача рульового керування.
Від’єднайте поворотну
магістраль охолоджувача робочої рідини підсилювача рульового керування від
бачка підсилювача рульового керування.
• Дайте рідині стекти в
придатну ємність.
4. Помістіть кінець
поворотного трубопроводу охолоджувача робочої рідини підсилювача рульового
керування в придатну ємність.
5. Підніміть і зафіксуйте
автомобіль.
6. Роз’єднайте
штекерний роз’єм датчика положення колінчатого вала (СКР).
7. Опустіть автомобіль
настільки, щоб колеса автомобіля піднялися над підлогою, щоб дати рульовому
колесу можливість повертатися від упора до упора.
8. При доливанні
робочої рідини в бачок підсилювача рульового керування переконаєтеся в тому, що
робоча рідина чиста. Не допускайте збовтування робочої рідини перед її
використанням. Щоб зменшити рівень насичення рідини повітрям, переливайте її в
бачок повільно. Рівень рідини варто перевіряти при перебуванні рідини в
холодному стані.
Залийте в бачок
підсилювача рульового керування робочу рідину до відмітки MAX.
9. Не провертайте
двигун безперервно протягом більш, ніж 30 секунд, тому що це може привести до
виходу стартера з ладу.
При провертанні двигуна
протягом проміжку часу, що не перевищує 30 секунд, поверніть рульове колесо від
упора до упора.
• Скориставшись
допомогою іншого техніка, додайте 1 літр чистої робочої рідини, такої, як
робоча рідина підсилювача рульового керування.
10. Почекайте 60
секунд, щоб дати стартеру можливість охолонути.
11. При провертанні
двигуна протягом наступних 30 секунд, повертайте рульове колесо від упора до
упора.
• Скориставшись
допомогою іншого техніка, додайте 0,6 літра чистої робочої рідини, такої як
робоча рідина підсилювача рульового керування.
12. Після того, як уся
рідина буде залита, переключіть перемикач пуску двигуна в положення «OFF» («вимк.»).
13. Підніміть і
підіпріть автомобіль.
14. Зістикуйте
штекерний роз'їм датчика CKP.
15. Опустіть
автомобіль.
16. Зніміть заглушку з
бачка підсилювача рульового керування.
З'єднайте поворотний
трубопровід охолоджувача робочої рідини підсилювача рульового керування з
бачком підсилювача рульового керування.
17. Закріпіть бачок
підсилювача рульового керування на колісній арці.
18. Закріпіть
розширювальний бачок системи охолодження на колісній арці.
1. Закріпіть
розширювальний бачок системи охолодження.
2. Встановіть болт.
19. При заливанні
робочої рідини в бачок переконайтеся в тому, що рідина чиста. Не збовтуйте її
перед використанням. Рідину варто переливати у бачок повільно, щоб мінімізувати
можливість її насичення газом. Рівень рідини варто перевіряти при перебуванні
рідини в холодному стані.
Залийте рідину в бачок
до відмітки «MAX».
20. Запустіть двигун і
повільно поверніть рульове колесо до відказу в одну та іншу сторону.
21. Вимкніть двигун.
22. Перевірте рівень рідини. При необхідності долийте необхідну
кількість робочої рідини.
4.
Економічна частина
4.1
Техніко-економічне обґрунтування проекту організації поста ТО маршрутних
транспортних засобів на базі філії «Темп-Авто»
В даний час, у зв’язку з
переходом на нові ринкові відносини, організації змушені розширювати обсяг
виробничих робіт не лише у основній сфері діяльності, а і надавати додаткові
послуги, використовуючи свої виробничі потужності. Це призводить до значного
технічного переозброєння, збільшення потужностей та покращення структури виробництва.
Проте виконання великої кількості різноманітних робіт, як показує
життя, потребує не лише кількісного збільшення різного за призначенням
обладнання і механізмів, але і, головне, підвищення їх продуктивності. Один із
головних резервів підвищення продуктивності Ї це доцільна організація ремонтів
та технічного обслуговування, тобто необхідне термінове запровадження нових
форм і методів ремонту та обслуговування транспортних засобів.
Актуальним тепер постає завдання, яке полягає в тому, щоб
наявні капітальні вкладення в організацію ремонтної бази використовувались
найбільш раціонально, щоб знижувалась собівартість технічного обслуговування
автомобілів, а також зростала продуктивність праці та фондовіддачі на ремонтних
підприємствах та станціях технічного обслуговування. У досягненні цього
важливого завдання головна роль відводиться спеціалістам на місцях, в
розпорядженні яких знаходяться засоби механізації. Від їх умілого, економічно
обґрунтованого підходу при організації використання таких великих
капіталовкладень на ремонтних підприємствах, впровадження досягнень науки і
техніки, використання досвіду передових організацій будуть залежати успіхи
виконання намічених планів підприємством.
Визначення трудомісткості робіт.
Трудомісткість поста ТО маршрутних транспортних засобів на базі
філії «Темп-Авто» Ї це загальні річні трудові затрати в людино-годинах, які
визначаються за формулою:

де: Тосн Ї трудомісткість основних робіт, люд-год;
Тосн = Тосн.д + Тосн.то
Тосн.д, Тосн.то – трудомісткість основних прибирально-мийних
робіт, люд-год;
Тосн.д = 241,56 люд-год;
Тосн.то = 0,3 Nа * Тосн.то. а
де Nмаш – кількість автомобілів даного виду, Nа = 165;
Тосн.то. маш – середня трудомісткість операцій при виконанні ТО і
Р маршрутного транспортного засобу, які повинні виконуватись згідно системі ППР
Тосн.то. маш = 20 люд. год. (37% від загальної тривалості ТО і Р автомобіля).
Тосн.то = 0,37 * 165* 20 = 4800 люд. год.
Тосн = 241,56 + 4800 = 5041 люд.
год.
Тобл Ї трудомісткість ремонту
власного обладнання, люд-год;
Тобл = (0,06–0,08)*Тосн люд. год
Тобл = 0,07*5041 = 352.9 люд. год
Твід Ї трудомісткість на
відновлення та виготовлення деталей, люд – год;
Твід = (0,03–0,05)*Тосн люд. год
Твід = 0,04*5041 = 201.7,
люд. год
Тп.р. Ї трудомісткість по
ремонту пристосувань та інструментів, люд-год;
Тп.р. = (0,02 – 0,03) Тосн,
люд-год;
Тп.р. = 0,025*5041 = 126,0,
люд-год;
Тп.г. Ї трудомісткість на
різні потреби, замовлення підприємства, люд-год;
Тп.г. = (0,05 – 0,08) Тосн,
люд-год;
Тп.г. = 0,06*5041 =
302,5, люд-год;
Тзаг = 5041+352,9+201,7+126,0+302,5= 10627,5 люд-год;
Визначення вартості валової продукції.
Вартість всієї валової продукції поста ТО
маршрутних транспортних засобів на базі філії «Темп-Авто» визначається на
основі договірних цін, що існують в ринкових умовах з кожного виду ТО і ремонту
за формулою:
Свп = У Сто_д_і*Нді
де: Свп Ї загальна вартість валової продукції підприємства за договірними
цінами, грн;
Нді Ї кількість і-го виду автомобілів, що підлягають ТО, шт.
Сто_д_і Ї вартість одиниці ТО і-того
виду автомобіля, грн;
Вартість
одиниці робіт по обслуговуванню визначається, як відношення трудомісткості
діагностування до трудомісткості капітального ремонту при постійній вартості
одиниці трудомісткості даного виду виробів за формулою:
Сто_і = Ск_і * Тто_і / Тк_і
де: Тто_і, Тк_і Ї періодичність відповідно ТО або
діагностування і капітального ремонту, (дод. 3 [16]);
Визначення вартості валової продукції поста
ТО маршрутних транспортних засобів на базі філії «Темп-Авто».

Сді = 0,12 * Сто3 = 0,12 * 2366,67 =
284,00 грн.
Сто_д_і = 284,00 грн.
Свп = 284,00* 165 = 162208,2 грн.
Сдн Ї вартість продукції, додатково наданої постом ТО маршрутних
транспортних засобів на базі філії «Темп-Авто» за замовленнями, грн.
Сдн = 0,5 * Тпг = 0,5*302,5= 151,25 грн.
Визначення річної програми поста ТО маршрутних транспортних
засобів на базі філії «Темп-Авто».
Кількість умовних обслуговувань визначається за формулою:
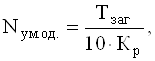
де: Кр – коефіцієнт, що враховує розмір відділення, Кр=0,97, с. 8
[18]
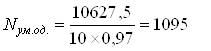
Визначення кількісного складу поста ТО маршрутних транспортних
засобів на базі філії «Темп-Авто».
Визначення кількісного складу основних виробничих робітників.
Загальна кількість основних виробничих робітників
визначається за формулою: Росн = Тзаг / (Фдр*Кпн)
Росн = 10627,5 / (1774,08*1,0) = 2,84
Приймаємо Росн =3 робочих.
Визначення кількості допоміжних працівників:
Рдоп = 0 робочий.
Визначення кількості інженерно-технічного персоналу:
Рітр = 1 інженер.
Визначення кількісного складу молодшого обслуговуючого персоналу:
Рмоп = 0,25 ставки прибиральниці.
Визначення загального складу робітників поста ТО маршрутних
транспортних засобів на базі філії «Темп-Авто»:
Рзаг = Росн+Роп+Р_ітр+Рмоп = 3+0+1+0,25 = 4,25 ставки,
Визначення загальної площі та кубатури поста ТО маршрутних
транспортних засобів на базі філії «Темп-Авто».
Fпід = 54 м2.
Vп = Fпід * h_під = 54*8,4 = 291,6 м3.
4.2 Визначення
загальної суми капітальних вкладень
Загальна сума капітальних вкладень в основні виробничі
фонди підприємства визначається за формулою:

де: Квир – капітальні
вкладення на будівництво приміщень виробничого призначення, визначаються за
формулою:
Квир = 18*Vп = 18*5448,2 =36083,2 грн.
Коб – вартість обладнання і його монтаж,
визначається за формулою:
Коб = 0,8*Квир = 0,8*136083,2 = 108864,2 грн.
Кпр.і. – вартість
пристосувань, інструментів, визначається за формулою:
Кпр.і = 0,11*Коб = 11975,5 грн
Кінв. – вартість господарського
інвентарю, визначається за формулою:
Кінв = 0,04*Коб = 4355,5 грн
Кзаг = 136083,2 + 108864,2+11975,5+4355,5 = 181273,6 грн.
4.3 Визначення
собівартості одиниці умовного обслуговування
Визначення собівартості одиниці умовного обслуговування за
фактичними затратами.
Собівартість одиниці умовного обслуговування за фактичними
затратами визначається за формулою:
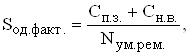
де: Сп.з.
– прямі затрати, грн./од.;
Сн.в. – накладні
витрати, грн./од.;
Визначення прямих затрат.
В підприємствах технічного сервісу у прямі затрати входять:

де: Ззаг.вир. роб.
Ї загальна заробітна плата тільки виробничих робітників,
грн.
Сз.ч. Ї вартість запасних частин,
грн.;
См. Ї вартість матеріалів, грн.;
Визначення загальної заробітної плати в прямих затратах.
Загальна заробітна плата виробничих робітників визначається
за формулою:
Ззаг.вир. роб. = Зосн. + Здод + Знарах
де: Зосн. Ї основна заробітна
плата виробничих робітників, грн.;
Здод. Ї додаткова заробітна плата виробничих робітників,
грн.;
Знарах. Ї нарахування на заробітну
плату виробничих робітників, грн.;
Визначення основної зарплати виробничим робітникам. Вона
визначається за формулою:

де: Сг. Ї
середньо-годинна тарифна ставка робітника, приймається в межах 3,8 розряду, що
відповідає 1 грн./год;
Кд. Ї коефіцієнт доплати за додатковий час
роботи, Кд.=1,075, с. 13 [18].
Трм = Фд.р. * Рзаг =1774,08*4,25 = 7539,84
Зосн = 7539,84*1*1,075 = 8105,3 грн.
Визначення додаткової заробітної плати іншим робітникам за
формулою:
Здод = 0,1*Зосн = 0,1* 8105,3 = 810,5 грн.
Визначення нарахування на заробітну плату виробничим
робітникам за формулою:
Знарах = 0,52*(Зосн+Здод) = 0,52*(8105,3+810,5) = 4634,2 грн.
Визначення вартості запасних частин, вузлів та агрегатів в
прямих затратах за формулою:
Сз.ч. = T*C*n*Кпод,
де: t, Ї
середній час роботи кожної машини в рік;
С, Ї вартість витрат запасних частин на
годину роботи автомобіля, грн.;
n Ї кількість автомобілів данної марки, шт.;
Кпод. Ї коефіцієнт подорожчання, Кпод.
=1,3, с. 4 [];
Сз.ч. = 2000*0,043*800*1,3 = 89440 грн.
Визначення вартості матеріалів та нафтопродуктів на
ремонтні цілі по формулі:
См = 0,1* Сз.ч. = 0,1*89440 = 8944,00 грн.
Ззаг.вир. роб. = 8105,3+810,5+4634,2 =
13552,11 грн.
Сп.в. = 13552,11 + 89440,0+8944,0=111936,11 грн.
Визначення накладних витрат.
На ремонтних підприємствах накладні витрати складають
значно більшу частину у порівнянні з прямими. Вони складаються в основному з
трьох складових частин і визначаються по формулі:

де: Сз.в. Ї загальновиробничі витрати, грн.;
Сз.г. Ї загальногосподарські витрати, грн.;
Спзв. Ї позавиробничі витрати, грн.
Визначення суму загально-виробничих витрат за формулою:

де: Зітр.
Ї заробітна плата інженерно-технічного персоналу, допоміжних робітників, молодшого
обслуговуючого персоналу за рік, грн. Вона визначається за допомогою табл. 5.1.
Сдм – вартість допоміжних
матеріалів.
Вартість допоміжних матеріалів береться в межах 10% від вартості
матеріалів прямих витрат за формулою:
Сд.м. = 0,1*См. = 0,1*8944 = 894,4 грн.
Са – річна сума амортизаційних
відрахувань визначається виходячи з балансової вартості основних фондів та
річних норм відрахувань, які дорівнюють:
Для будівель – 2,5…7%;
Для обладнання – 6…10%;
Для інструментів та пристосувань – 12…18%
Таблиця 4.1.
Визначення фонду зарплати ІТР, допоміжних робітників,
службовців та МОП
№ п/п |
Назва |
К-сть |
Середньомісячна зарплата, грн./
прац. |
Річний фонд зарплати, грн. |
1 |
ІТР |
1 |
650 |
7800 |
2 |
Допоміжні робітники |
0 |
0 |
0 |
3 |
МОП |
0,25 |
300 |
900 |
Разом основна зарплата |
8700 |
4 |
Додаткова зарплата 10% від основної |
870 |
5 |
Нарахування 52% від основної та додаткової зарплати |
4976,4 |
6 |
Всього річний фонд зарплати |
14546,4 |
Са = Са.буд. + Са.обл. + Са.ін-т.,
Са = 0,05*13608+0,08*10886,4+0,15*1197,50 = 1730,94 грн.
Сбр – річна сума відрахувань на
біжучий ремонт основних фондів. Визначається виходячи з балансової вартості
основних фондів та річних норм відрахувань, які дорівнюють:
Для будівель – 3%;
Для обладнання – 4…7%;
Для інструментів та пристосувань – 2…5%
Сбр. = Сбр.буд. + Сбр.обл. + Сбр.інст.,
Сбр. = 0,03*13608+0,055*10886,4+0,035*1197,50 = 1048,91 грн.
Су.о.ф. – витрати на утримання
основних фондів:
Для будівель – 0,5%;
Для обладнання – 0,5%;
Для інструментів та пристосувань 86 грн. на одного працюючого.
Су.о.ф. = Су.о.ф.буд. + Су.о.ф. обл. + Су.о.ф. інст.,
Су.о.ф. = 0,005*13608,0+0,005*10886,4+86*4 = 466,47 грн.
Св.ел – витрати на
електроенергію. Повна вартість витрат на електроенергію визначається за
формулою:

де: Цод Ї вартість 1 кВт, Цод=0,19 грн
Рсил Ї витрати на
електроенергію для силових потреб, визначаються за формулою:
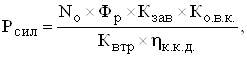
де: No Ї потужність всіх двигунів,
No=5,5 кВт на одного виробничого робітника, с. 15 [18];
Кзав Ї коефіцієнт завантаження, Кзав=0,85, с. 15 [18];
Ко.в.к. Ї коефіцієнт одноразового включення, Ко.в.к.=0,7, с. 15
[18];
Квтр Ї коефіцієнт втрат в мережі, Квтр=0,96, с. 15 [18];
Ŋк.к.д. Ї коефіцієнт корисної дії, Ŋк.к.д.=0,85, с. 15
[18];

Росв Ї витрати на освітлення, визначаються за формулою:
Вт
де: No Ї встановлена потужність світильників, 100 Вт на
1 м2 площі, с. 15 [18];
Фр Ї річний фонд роботи світильників, Фр=700
годин, с. 15 [18];
Квідк Ї коефіцієнт відключення, Квідк=0,85, с. 15 [18];
Росв = 100*90*700*0,85/1000 = 5355,0 кВт
Св.ел = (21334,4+5355,0)*0,19 = 5072,89 грн.
Спар Ї витрати на технологічну воду, пар, повітря беруться 0,667
грн. на 1 умовне обслуговування, визначаються за формулою:
Спар = 0,667*Nум.рем = 0,667*630 = 420,28 грн.
Спбт Ї витрати на побутові потреби, беруться 14 грн на одного
робітника та 6 грн на кожного іншого з персоналу в рік,
Спбт = 14*3+6*1,25 = 49,5 грн.
Сопал Ї витрати на опалення, беруться 4 грн. на 1м3
об’єму будівель,
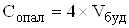
Сопал = 4*756 = 3024,0 грн.
Срац Ї витрати на раціоналізацію беруться 50 грн. на кожного
працюючого на підприємстві,
Срац=50 * 4 = 200 грн;
Сох.пр Ї витрати на охорону праці беруться 30 грн на кожного
працюючого на підприємстві,
Сох.пр = 30*4,25 = 127,5 грн.;
Сп.т Ї витрати поштово-телеграфні беруться 100 грн. на кожного ІТР
та службовця в рік,
Сп.т = 100 грн.;
Сінші – інші витрати беруться 3% від усіх попередніх витрат,
Сінші = 269,82 грн.
Тоді
Сзв. = 5072,89+420,28+49,5+3024,0+200+127,5+100,0+269,8 = 9263,99
грн.
Визначення загальновиробничих витрат «Сз.г.»
Загальновиробничі витрати включають:
–
витрати на утримання
адміністративно – господарчого персоналу;
–
витрати на утримання інших
організацій;
–
витрати на утримання
транспорту;
–
витрати на утримання
будівель та споруд адміністративно-господарського характеру;
–
витрати на утримання
лабораторій, пожежної охорони та інші витрати пов'язані з управлінням,
організацією та обслуговуванням господарства.
Загальновиробничі витрати приймають в розмірі 300–500% від
основної зарплати робітників за формулою:
Сз.г. = 5*Ззаг.вир. роб. = 5*13552,11 = 67760,55 грн.
Визначення позавиробничих витрат «Спзв.»
Позавиробничі витрати включають витрати на
наукову-випробувальну роботу, технічну пропаганду, підготовку кадрів.
Позавиробничі витрати приймаються в межах 30–50% від зарплати виробничих
робітників за формулою:
Спзв. = 0,5*Ззаг.вир. ро. = 0,5*13552,55 = 6776,06 грн.
Сн.в. = 9263,99 + 67760,54 + 6776,05 = 83800,58 грн.
= (111936,1 + 83800,58) / 1095 = 626,8 грн/од.
Визначення повної собівартості всіх робіт по технічному
обслуговуванню:
Спов = Сп.з.+ Сн.в. = 11193,1 + 8380,58 = 122480,9 грн.
Визначення собівартості одиниці умовного обслуговування по
відпускних цінах:

4.4 Визначання економічної ефективності
організації поста ТО маршрутних транспортних засобів на базі філії «Темп-Авто»
Визначення прибутку поста ТО маршрутних транспортних засобів на
базі філії «Темп-Авто».
Прибуток – це різниця між вартістю
товарної продукції та її собівартістю.
Пр = Св.п. – Спов,
Пр = 162208,2 – 122480,9 = 39728 грн.
Визначення рівня рентабельності поста по
технічному обслуговуванню з реалізованої продукції
Це
відсоткове відношення прибутку до собівартості товару
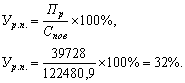
Визначення рівня рентабельності поста по технічному обслуговуванню по виробничих фондах
Це процентне відношення прибутку до
вкладених основних та виробничих фондів
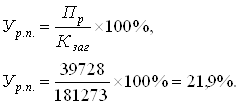
Визначення продуктивності праці

де: Рзаг = 3 – загальна кількість працюючих, чол.
Визначення коефіцієнта використання виробничих площ

Визначення коефіцієнта фондовіддачі

Кф – випуск продукції в грн. на 1 грн.
капіталовкладень.
Визначення коефіцієнта загальноекономічної
ефективності.

Визначення строку окупності поста ТО маршрутних транспортних
засобів філії «Темп-Авто».
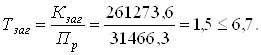
Основні техніко-економічні показники представлено в табл. 4.2
Таблиця 4.2. Основні техніко-економічні показники поста ТО
маршрутних транспортних засобів
№ |
Назва
показників |
Од.
виміру |
Значення
показника |
1. |
Загальні
капіталовкладення Кзаг |
грн. |
181273,6 |
2. |
Загальна
трудоємкість Тзаг |
люд.-години |
10627,5 |
3. |
Вартість
валової продукції Свп |
грн. |
162208,2 |
4. |
Виробнича
програма в умовних обслуговуваннях, Nум.рем |
одиниці |
1095 |
5. |
Повна
собівартість всіх робіт з технічного обслуговування Спов |
грн. |
122480,9 |
6. |
Собівартість
одиниці умовного обслуговування:
а)
за фактичними витратами Sод.факт
б)
за відпускними цінами Sод.від
|
грн./од.
грн./од.
|
626,8
752,2
|
7. |
Визначення
прибутку поста технічного обслуговування Пр |
грн. |
39728 |
8. |
Рівень
рентабельності Урп |
% |
22 |
9. |
Визначення
продуктивності праці Ппр |
грн./1
працюючого |
4552 |
10. |
Визначення
коефіцієнту фондовіддачі Кф |
грн./1
грн. |
1,70 |
11. |
Визначення
коефіцієнта загальної економічної ефективності Езаг |
|
1,20 |
12. |
Визначення
строку окупності капітальних вкладень |
років |
1,5 |
Висновки
В процесі виконання дипломного проекту ми прийшли до висновків:
1.
В
організаційно-розрахунковій частині проекту ми на основі кількісного складу
маршрутних транспортних засобів, що планується централізовано обслуговувати на
базі філії «Темп-Авто», а також враховуючи виробничо-технічну базу та наявність
виробничих площ на підприємстві провели розрахунок виробничої програми та
визначили трудоємкість робіт по ТО. В результаті розрахунків ми одержали
значення трудомісткості робіт по централізованому ТО маршрутних транспортних
засобів 10627,05 люд.-год, для чого необхідно організувати на базі філії «Темп-Авто»
один пост ТО суміщений з проведенням діагностичних робіт. Тут же намічено план
заходів та приведено перелік технологічного обладнання для вказаного поста.
2.
Враховуючи досить велику
частку розбірно-збірних робіт при виконанні процесів ТО, ми на основі аналізу
конструкцій різьбозгвинчуючого обладнання та існуючих методик його розрахунку
ми провели розрахунок планетарної передачі гайковерта, який може бути
використаний при виконанні операцій по ТО і ремонту на станціях технічного
обслуговування.
3.
В технологічній частині
проекту нами розроблено документацію на процес технічного обслуговування
рульового керування, оскільки даний вузол є відповідальним за безпеку руху.
4.
Доцільність організації
поста ТО суміщеного з проведенням діагностичних робітна базі філії «Темп-Авто»
обґрунтована проведеними економічними розрахунками.
Література
1.
Шумик С.В. и др. Техническая эксплуатация автотранспортних
средств: Курсовое и дипломное проектирование: Учебное пособие /С.В. Шумик,
М.М. Болбас, Е.Н. Петухов: под ред. С.В. Шумика. – МН.:
Выш. шк., 1988. – 206 с.
2.
Савич Е.Л. Техническое обслуживание и ремонт легковых
автомобилей: Учеб. пособие /Е.Л. Савич, М.М. Болбас, В.К. Ярошевич;
Под общ. ред. Е.Л. Савича. – Мн.: Выш. шк., 2001. – 479 с.
3.
Марчук М.М. Технічна експлуатація
автомобілів: Навчальний посібник, – Рівне 1999. – 194 с.
4.
Канарчук В.Є. та ін. Основи технічного
обслуговування і ремонту автомобілів. У 3-х кн. Кн. 2. Організація, планування
й управління: Підручник/В.Є. Канарчук, О.А. Лудченко, А.Д. Чигринець.
– К.: Вища шк. 1994. -383 с.
5.
Техническая эксплуатация автомобилей /под ред. E.С. Кузнецова.
– М.: Транспорт, 1991. – 413 с.
6.
Ткачук В.Ф. Механізований
інструмент. – Рівне: НУВГП. 2005.-279 с.
7.
Малиновский А.Н. Планетарные передачи. – М.: Высшая школа.
1968.-130 с.
8.
Е.Я. Красковский, Ю.А. Дружинин, Е.М. Филатова
Расчет и конструирование механизмов приборов и вычислительных систем 2-е изд.
М.: Высш. шк., 1991.-408 с.
9.
Единая система конструкторской документации: Справочное пособие /С.С. Борушек,
А.А. Волков, М.М. Ефимова и др. М.: Издательство стандартов, 1989. –
352 с.
10.
Зеленков Г.И., Колясинский Б.С. Проектирование
предприятий по ремонту дорожно-строительных машин. – М.: Высшая школа, 1971. –
240 с.,
11.
Бабусенко С.М. Проектирование ремонтных предприятий. – М.:
Колос, 1981. – 285 с.
12.
Водолазов Н.К. Курсовое и дипломное проектирование по
механизации сельского хозяйства. – М.: Агропромиздат, 1991. – 335 с.,
13.
Воловик Е.Л. Справочник по восстановлению деталей. – М.:
Колос, 1981. – 351 с.,
14.
Гуревич Д.Ф., Зуев А.А. Эксплуатация оборудования ремонтных
мастерских. Л., «Колос» (Ленингр. отделение), 1975, – 367 с.
15.
Справочник инструментальщика. /И.А. Ординарцев, Г.В. Филиппов,
А.Н. Шевченко и др. – Л.: Машиностроение, 1987. – 846 с.,
16.
Справочник техника-конструктора. Изд. 3-е, перераб. и доп.
Самохвалов Я.А., Левицкий М.Я., Григораш В.Д. Киев, «Техніка», 1978. 592 с.
17.
Сухарев Э.А. Теория капитального ремонта машин. – Ровно:
РГТУ, 2001, – 195 с.
18.
ОНТП–01–91.
Общесоюзные нормы технологического проектирования предприятий автомобильного
транспорта. – М. Гипроавтотранс, 1991. -187 с.
19.
Табель технологического оборудования автотранспортных предприятий, –
К.: Минавтотранс УССР, 1984. -179 с.